LETNIA AKADEMIA TOYOTY, czyli internetowy przewodnik po Toyota Production System – cz. I
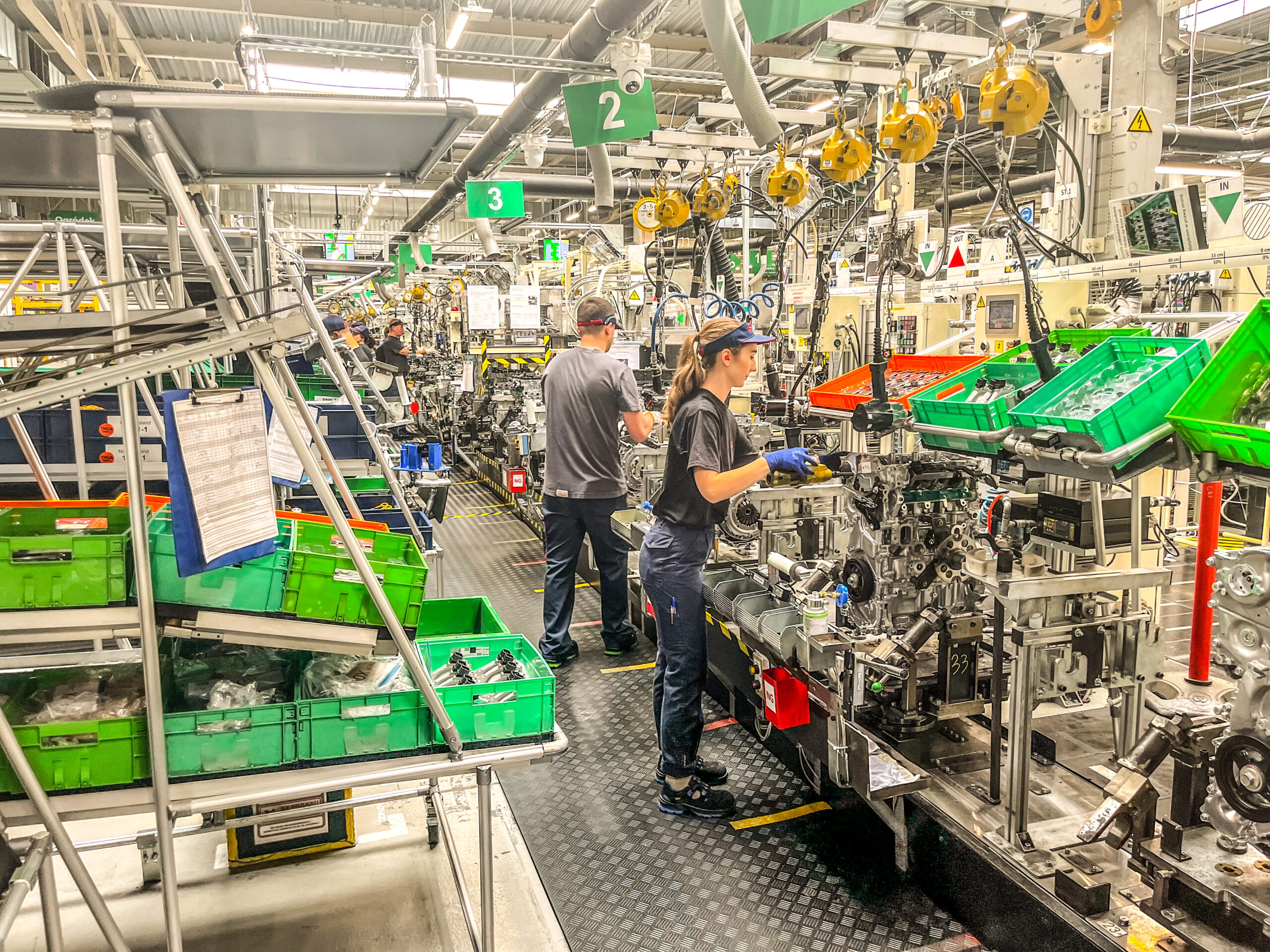
W fabrykach TOYOTY kładziemy nacisk na autorską filozofię firmy, znaną na całym świecie jako System Produkcyjny Toyoty, czyli TPS (Toyota Production System). Ale co dokładnie kryje się pod tymi trzema literami? Pewnego dnia w naszych głowach narodziła się myśl, że jako pracownicy Toyota Motor Manufacturing Poland chcemy mieć nasze własne opracowanie TPS. Tak narodził się Projekt LATO – Letnia Akademia Toyoty, czyli cykl edukacyjny poświęcony Toyota Production System, oparty na doświadczeniach z naszych fabryk w Jelczu-Laskowicach i Wałbrzychu. Stworzyliśmy więc cykl publikacji, które mogliście czytać na naszym LinkedInie, pracowniczym Instagramie oraz profilach Facebookowych fabryk w Jelczu i Wałbrzychu. Niestety lato dobiegło końca, a wraz z nim nasz projekt. Niemniej jednak to nie koniec naszej podróży przez świat Toyota Production System. Zapraszamy na podsumowanie naszego cyklu LATO!
JUST-IN-TIME: W SYSTEMIE PRODUKCYJNYM TOYOTY WSZYSTKO ODBYWA SIĘ DOKŁADNIE NA CZAS
Naszą podróż przez Systemy Produkcyjne Toyoty rozpoczęliśmy od jednego z jej filarów — filozofii Just-in-Time (dokładnie na czas). Jej założeniem jest produkcja tylko tego, co jest potrzebne, kiedy jest potrzebne, i w takiej ilości, jaka jest potrzebna. TOYOTA opracowała ten system, aby unikać produkcji nadwyżek, które zmuszają do kosztownego magazynowania. Dlatego produkcja danego silnika rusza dopiero w momencie, kiedy pojawi się na niego zamówienie. To nie tylko pozwala nam określić, do jakiego samochodu i w jakim kraju trafi dany silnik, ale także umożliwia bezpośrednie przekazywanie wyprodukowanych silników z produkcji do transportu.
Dzięki Just-in-Time unikamy marnowania czasu na niepotrzebne operacje, minimalizujemy ryzyko zmarnowania zasobów i eliminujemy koszty związane z nadmiernym magazynowaniem. Just-in-Time jest nieodłącznym elementem efektywności w naszych fabrykach TOYOTY.
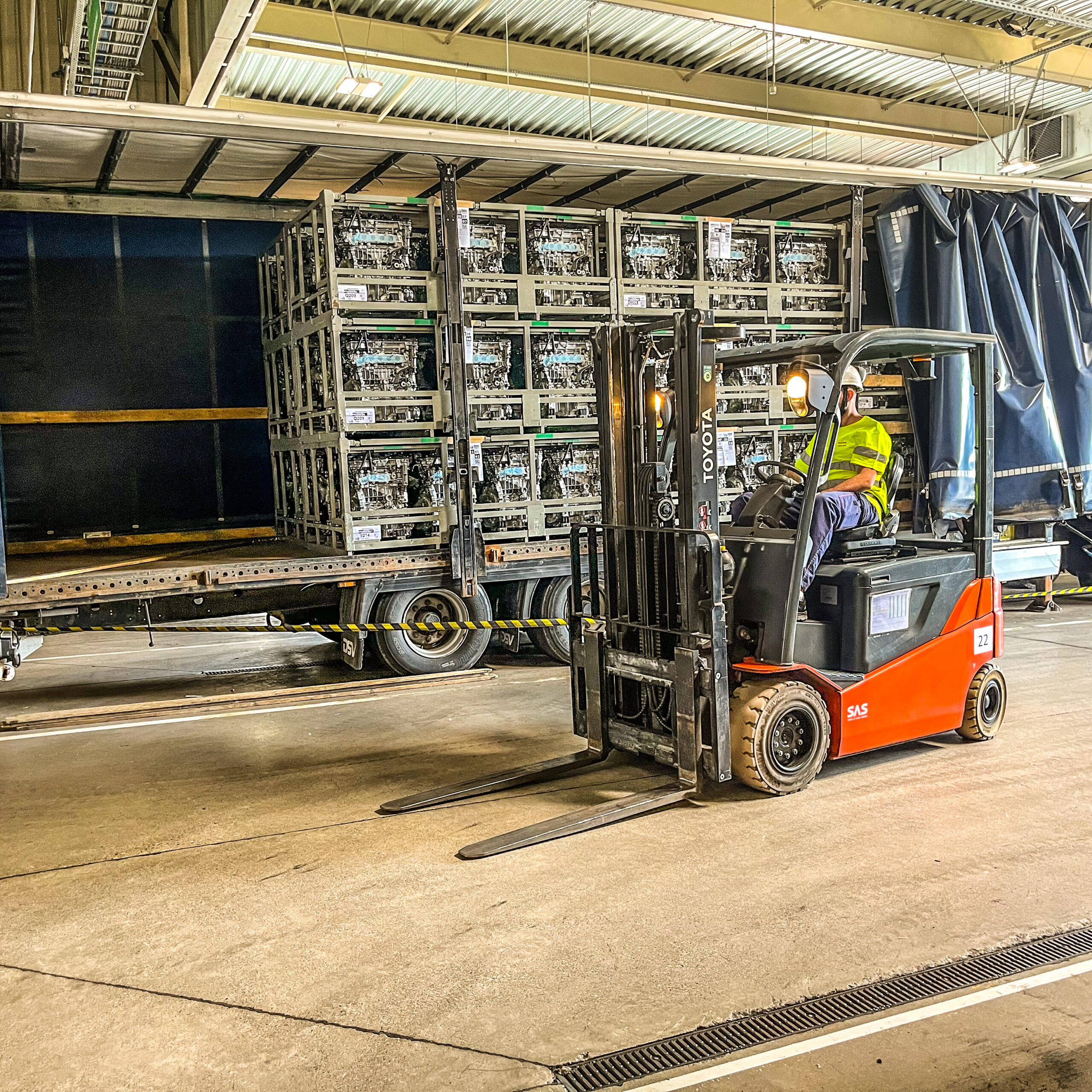
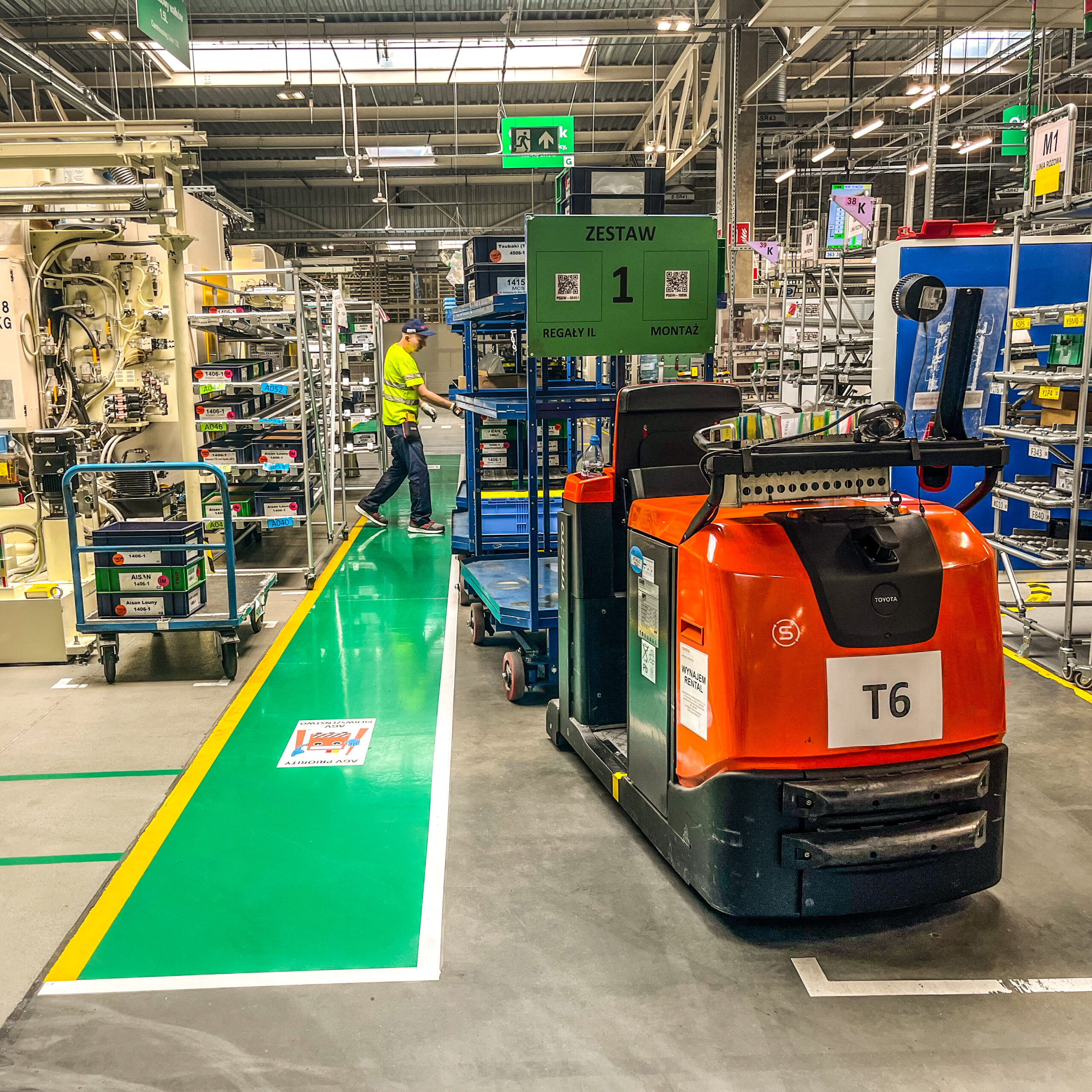
KANBAN: W TMMP EFEKTYWNIE ZARZĄDZAMY ZASOBAMI
Po przedstawieniu filaru TPS należy omówić poszczególne procesy, które umożliwiają jego funkcjonowanie. Pierwszym z nich jest Kanban (z j. japońskiego „szyld”), który w naszych procesach produkcyjnych oznacza wizualny system przekazywania informacji o zasobach. Najczęściej przyjmuje formę kart Kanban, które stanowią informację przekazywaną przez pracownika produkcji do działu logistyki, dotyczącą konieczności uzupełnienia komponentów na stanowisku w ilości adekwatnej do zapotrzebowania.
Pracownik przed rozpoczęciem pracy ma na swoim stanowisku przygotowane pudełko ze standaryzowaną ilością materiału potrzebnego do wykonania pracy. W momencie pobrania pierwszej części, pracownik przekazuje zawiadomienie w formie karty Kanban, o tym, co będzie potrzebował w następnej kolejności. Pracownik logistyki odbiera wiadomość, przygotowuje zamówienie i dostarcza je w odpowiednie miejsce jeszcze przed wyczerpaniem się poprzedniego materiału. Ten proces powtarza się zgodnie z ustalonym planem produkcji. Dzięki Kanbanowi pracownicy mogą skupić się na efektywnym wykonywaniu zadań, a system zarządzania zasobami staje się bardziej dynamiczny. Kanban to nie tylko narzędzie, to integralna część Toyota Production System. Zapobiega przestojom, zapewnia płynność produkcji oraz umożliwia efektywne zarządzanie zasobami.
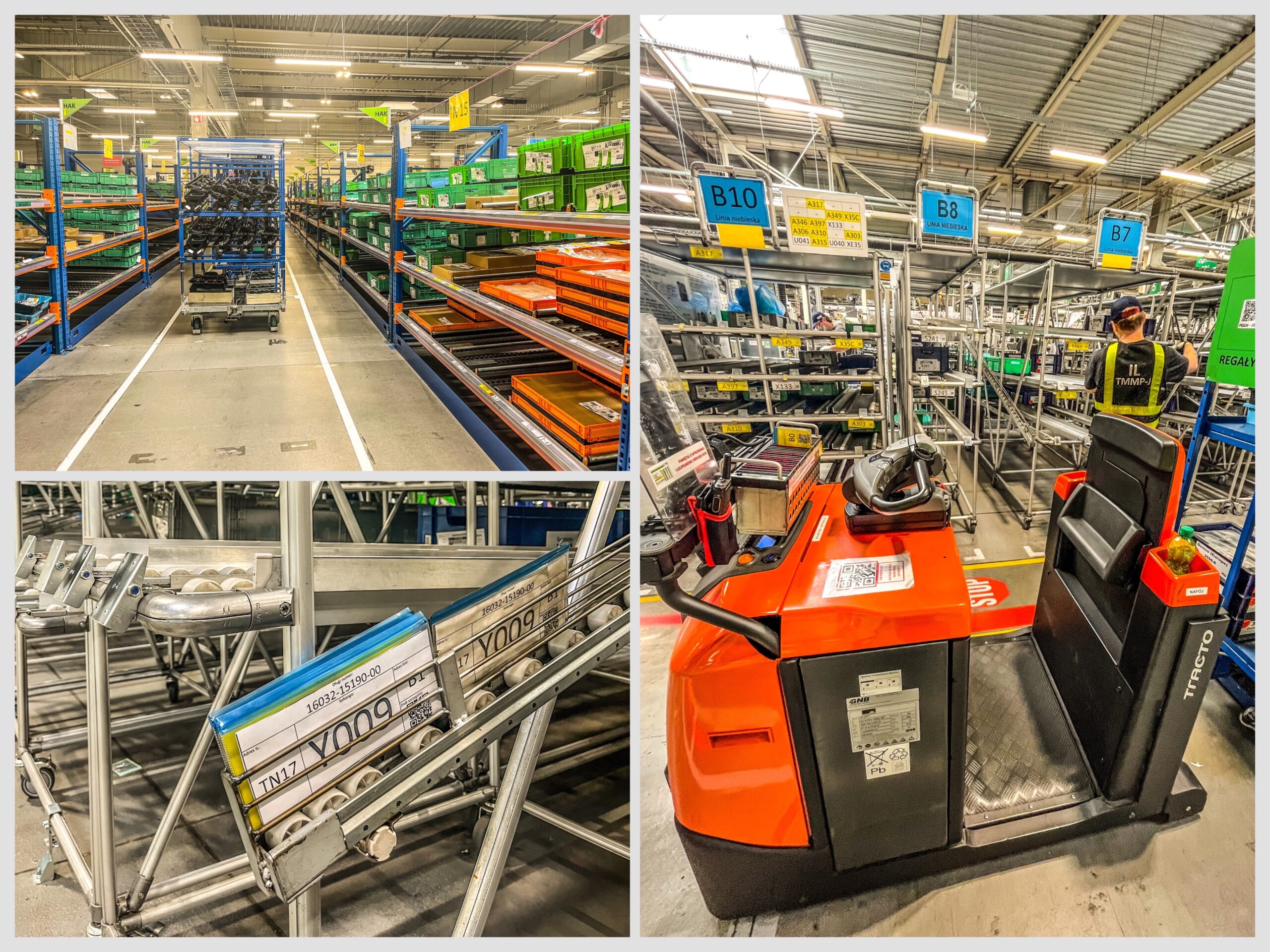
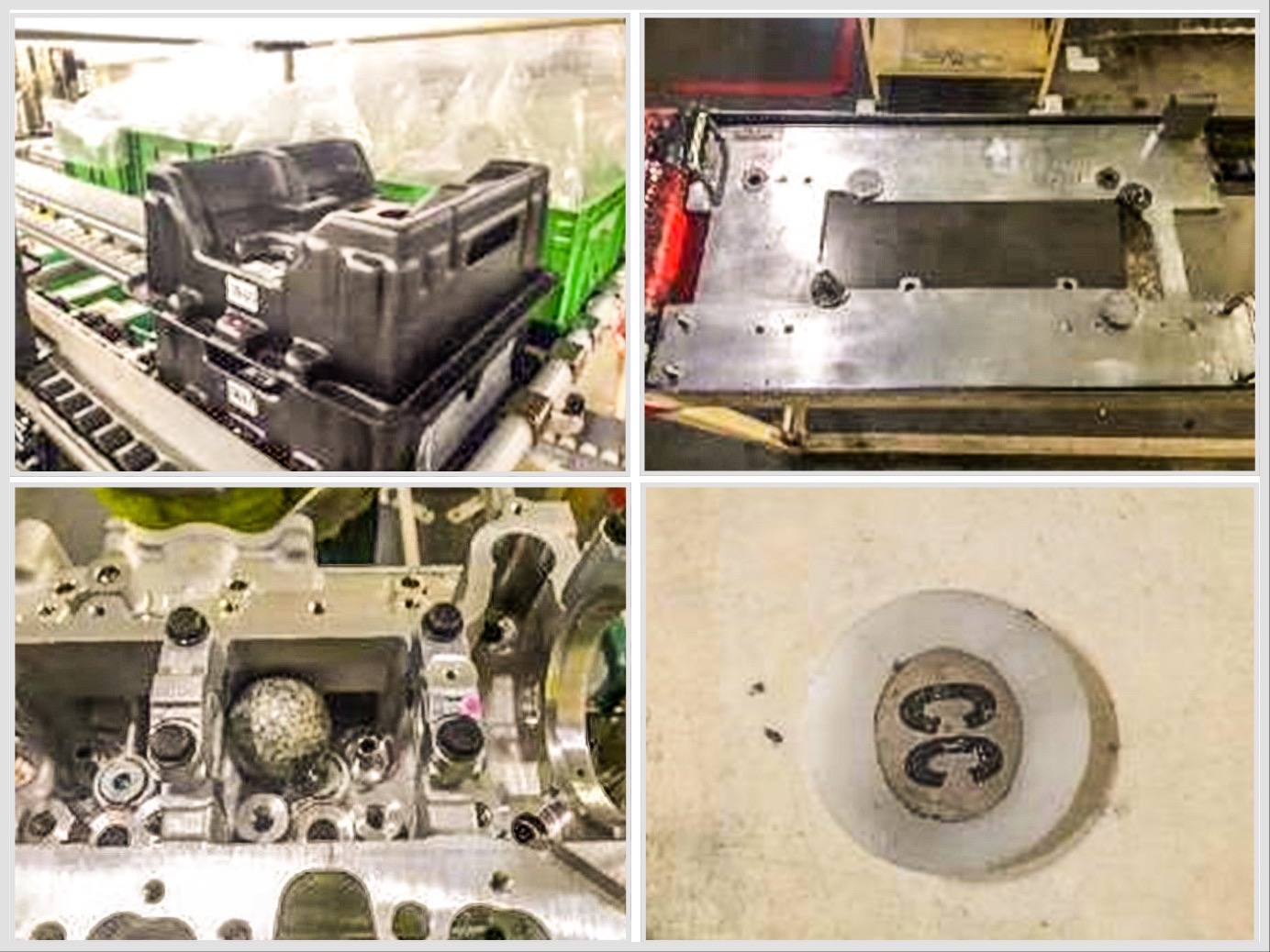
HEIJUNKA: ZOPTYMALIZOWANA PRODUKCJA WEDŁUG TPS
Ważne są dla nas zorganizowane i stabilne procesy produkcyjne, pozwalające pracownikom wykonywać zadania w spokoju, a maszynom utrzymywać stałe tempo pracy. W tym pomaga nam Heijunka (z j. japońskiego „wyrównanie”), zwana przez nas „wyrównaniem produkcji” lub „produkcją na przemian”. Głównym celem Heijunki jest dostosowywanie produkcji do bieżących potrzeb klienta,dlatego opracowaliśmy specjalne linie MIX, dostosowane pod produkcję różnych rodzajów silników. Dzięki temu nagła zmiana zapotrzebowania nie wymaga od nas zatrzymania produkcji i przeprowadzania czasochłonnego przezbrajania linii.
Odpowiadamy w ten sposób na realne wyzwanie, przed którym staje wiele firm. Często w fabrykach produkuje się nadmiar towaru, zakładając, że zapotrzebowanie klienta nie ulegnie zmianie. Jednak, gdy tak się dzieje, wyprodukowane nadwyżki zalegają w magazynie, generując niepotrzebne koszty i tracąc na wartości. Heijunka pozwala nam unikać takich sytuacji oraz produkować płynnie w różnych konfiguracjach.
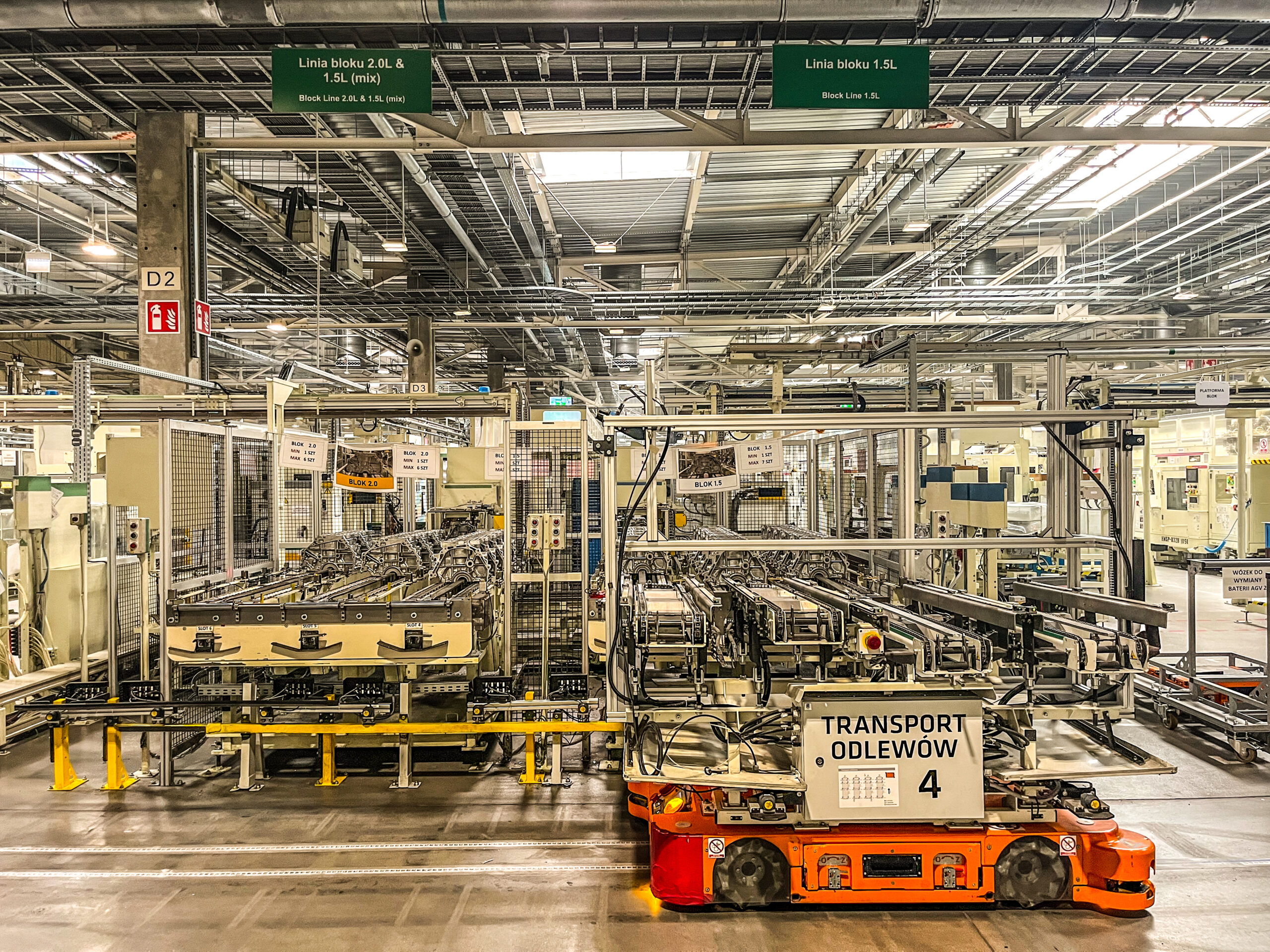
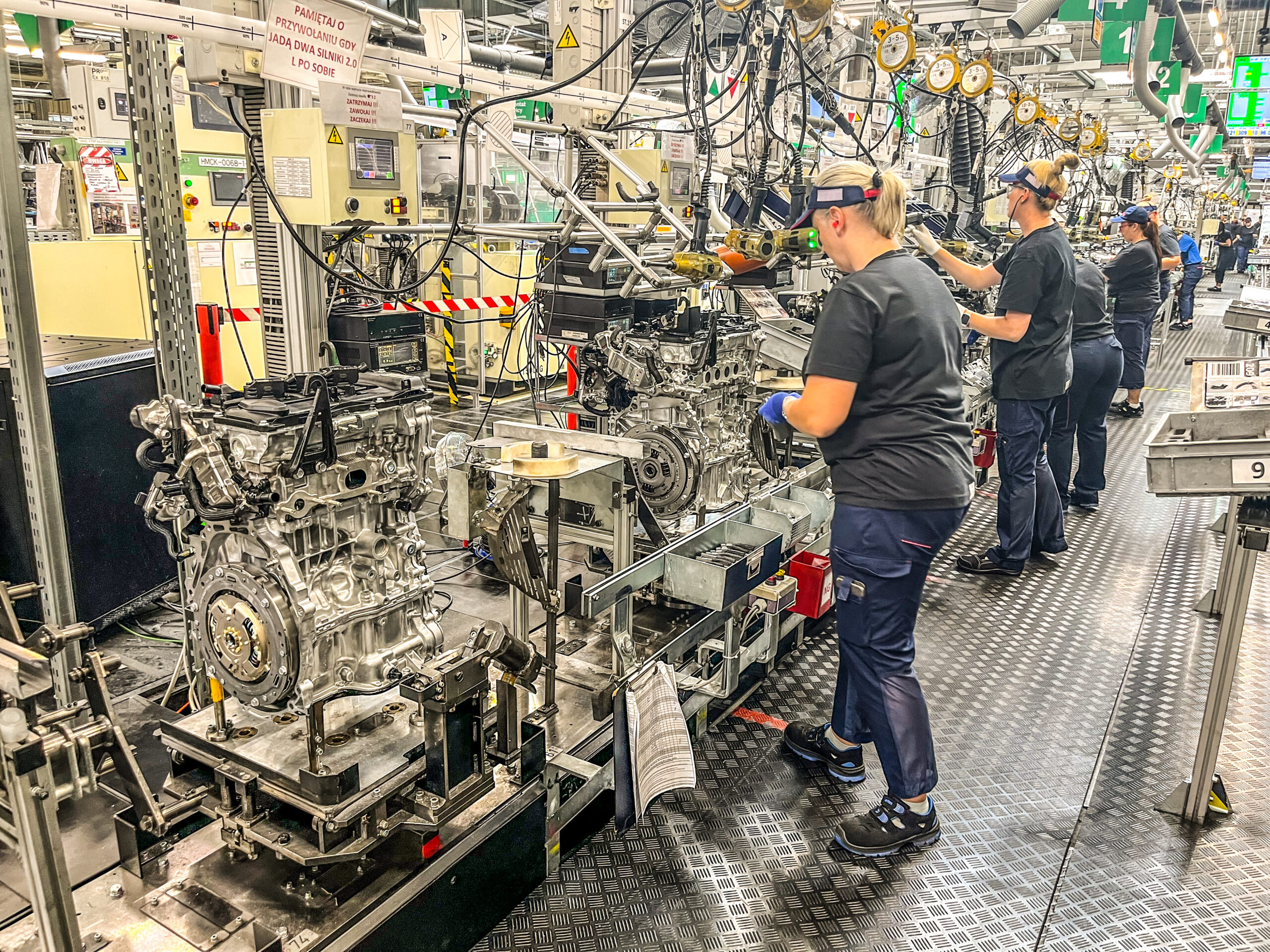
MUDA, MURI, MURA: TRZY WYZWANIA NA DRODZE DO NIEZAWODNEJ PRODUKCJI
Muda, Muri, Mura z j. japońskiego to kolejno: marnowanie, przeciążenie i nierówność. Te trzy pojęcia określają trzy największe przeszkody na drodze do osiągnięcia niezawodnej produkcji. Dlatego jednym z głównych celów TPS jest eliminacja procesów, które prowadzą do marnowania zasobów, nierówności w poszczególnych obszarach produkcji oraz przeciążenia pracowników i maszyn.
Muda z j. japońskiego oznacza marnowanie, ale w słowniku Systemu Produkcyjnego Toyoty odnosi się do wszystkich czynności, które nie dodają żadnej wartości. W przypadku Mudy można wyróżnić 7 rodzajów strat:
- Nadprodukcja – wytwarzanie ponad zapotrzebowanie.
- Zapasy – zasoby składowane na wypadek sytuacji, która może nigdy się nie wydarzyć.
- Oczekiwanie – przestoje, które wynikają ze złego zarządzania bądź przyczyn niezależnych.
- Nadmierne przetwarzanie – maszyna bądź człowiek pracują więcej niż wymaga tego proces.
- Transport – czasochłonne przemieszczanie przedmiotów.
- Zbędny ruch – poruszanie się intensywniej i częściej niż jest to konieczne.
- Błędy – produkty, które nie spełniają oczekiwań klientów.
Muri tłumaczymy jako przeciążenie. W ten sposób mówi się o wszystkich czynnościach, które nadmiernie obciążają pracownika bądź maszynę. Mogą być to np.:
- nadgodziny wynikające ze źle zaplanowanej pracy;
- nieergonomiczne stanowisko pracy;
- kumulacja wielu zadań w jednym momencie.
Mura to nierówność, są to więc wszystkie rzeczy doprowadzające do nierównomiernej produkcji na różnych obszarach pracy, np.:
- nierównomierne tempo pracy;
- nierównomierny podział obowiązków;
- brak standardów i zasad.
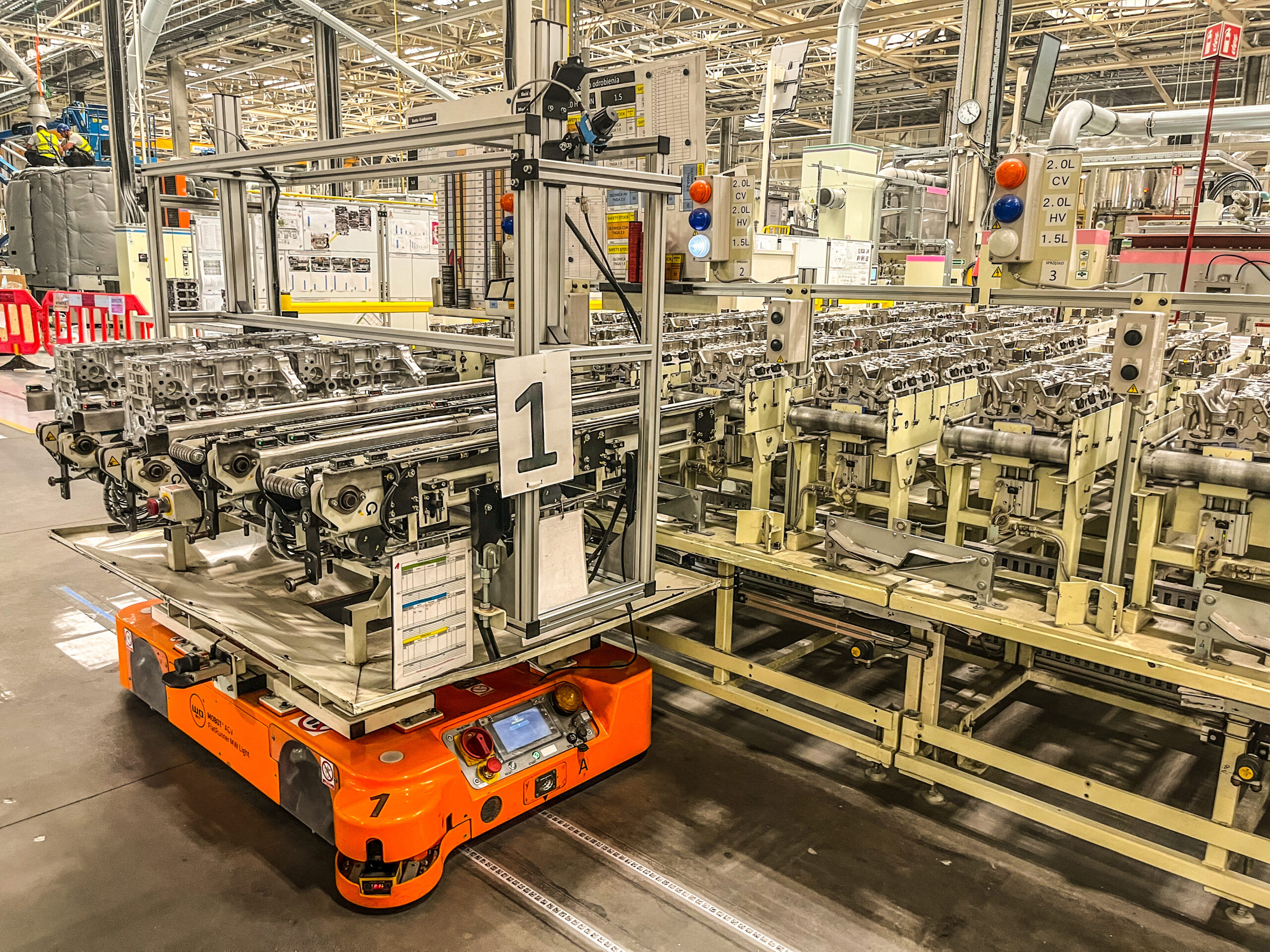
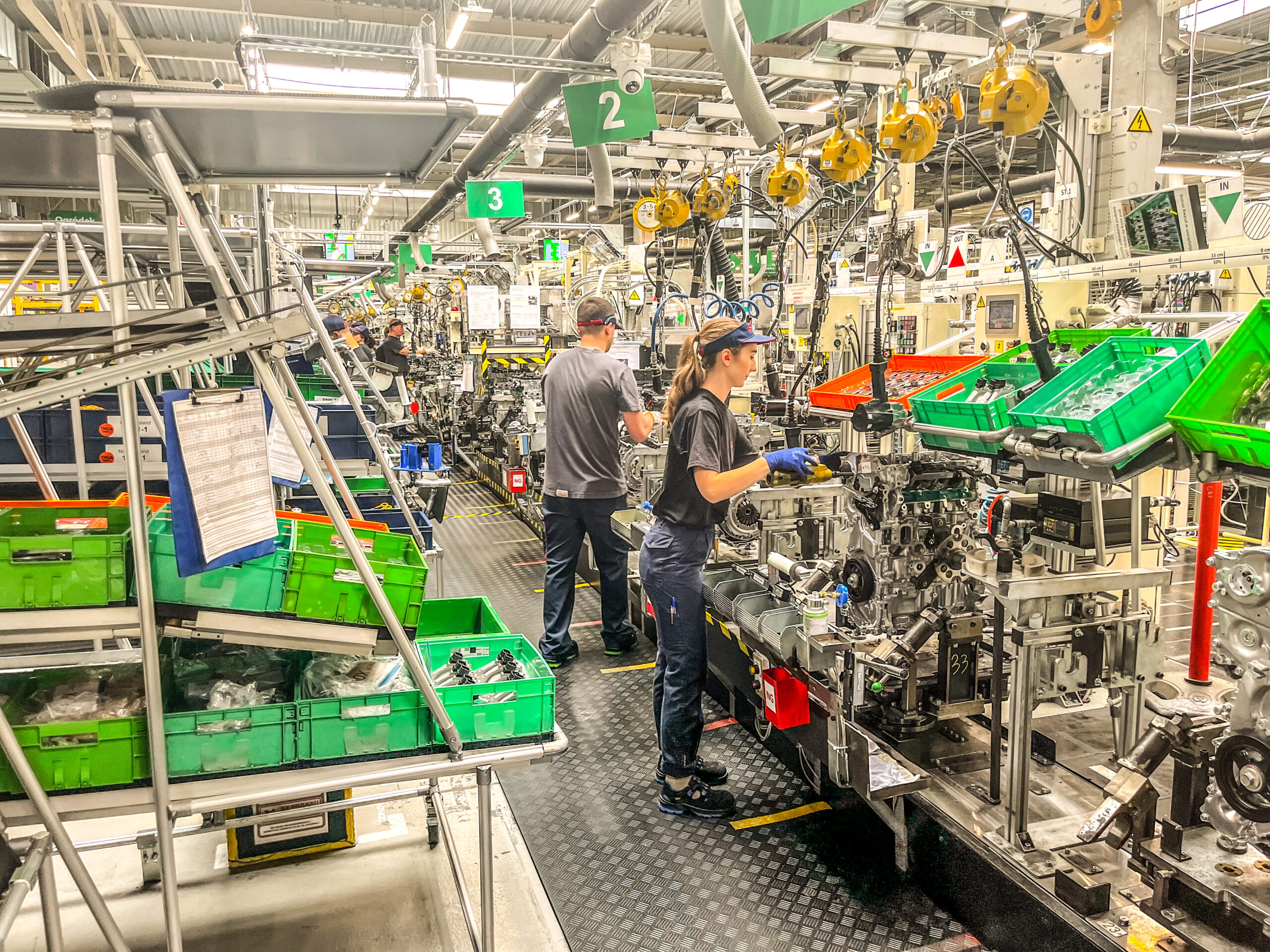
JIDOKA I POKA-YOKE: AUTOMATYZACJA Z LUDZKĄ TWARZĄ W TPS
Jidoka (z j. japońskiego „automatyzacja z ludzką twarzą”) stanowi drugi, obok Just- in- Time, filar Systemu Produkcyjnego Toyoty. Jego podstawowym systemem jest Poka-Yoke (z j. japońskiego „zapobiegać błędom”), czyli mechanizmy zabezpieczające zastosowane w procesach produkcyjnych, mające na celu wykrywanie i zapobieganie nieprawidłowościom na czas.
Jidoka to forma automatyzacji, która nie ma na celu zastąpienia pracownika, lecz współpracę z nim w celu osiągnięcia wyższej efektywności i jakości w procesach produkcyjnych. Opracowano ją w TPS, aby spełnić kluczową dla nas zasadę: zero niesprawnych silników.
W celu zapobieganiu powstawaniu niesprawnych i niejakościowych silników, wprowadzono Poka-Yoke (system zapobiegania błędom, zanim do nich dojdzie). Jest on ściśle powiązany ze wspomnianą wcześniej Mudą, czyli marnowaniem. Dzięki niemu możemy wykrywać wady już na etapie produkcji, zapobiegając marnowaniu zasobów, pracy i czasu pracowników.
Jakie są formy Poka-Yoke?
- Roboty sprawdzające silniki wykorzystują wgrane schematy silników do wykrywanie odstępstw od normy.
- Czujniki w maszynach i na stanowiskach, przypominające pracownikom o poborze odpowiedniej liczby części we właściwym momencie.
- Narzędzia naprawcze, umożliwiające naprawę usterki.
- Nasze własne oczy, ponieważ Poka-Yoke posiada „ludzką twarz”.
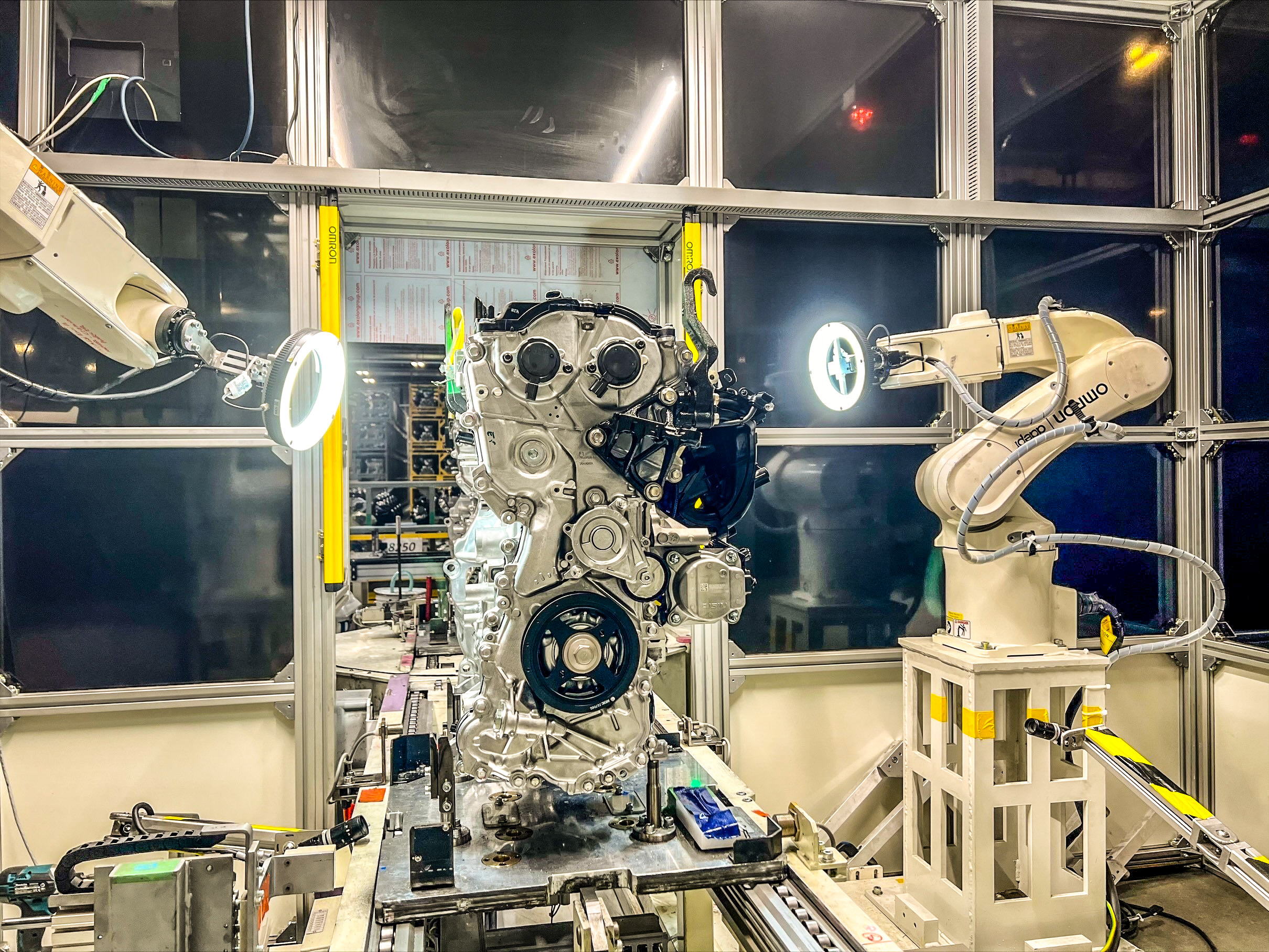
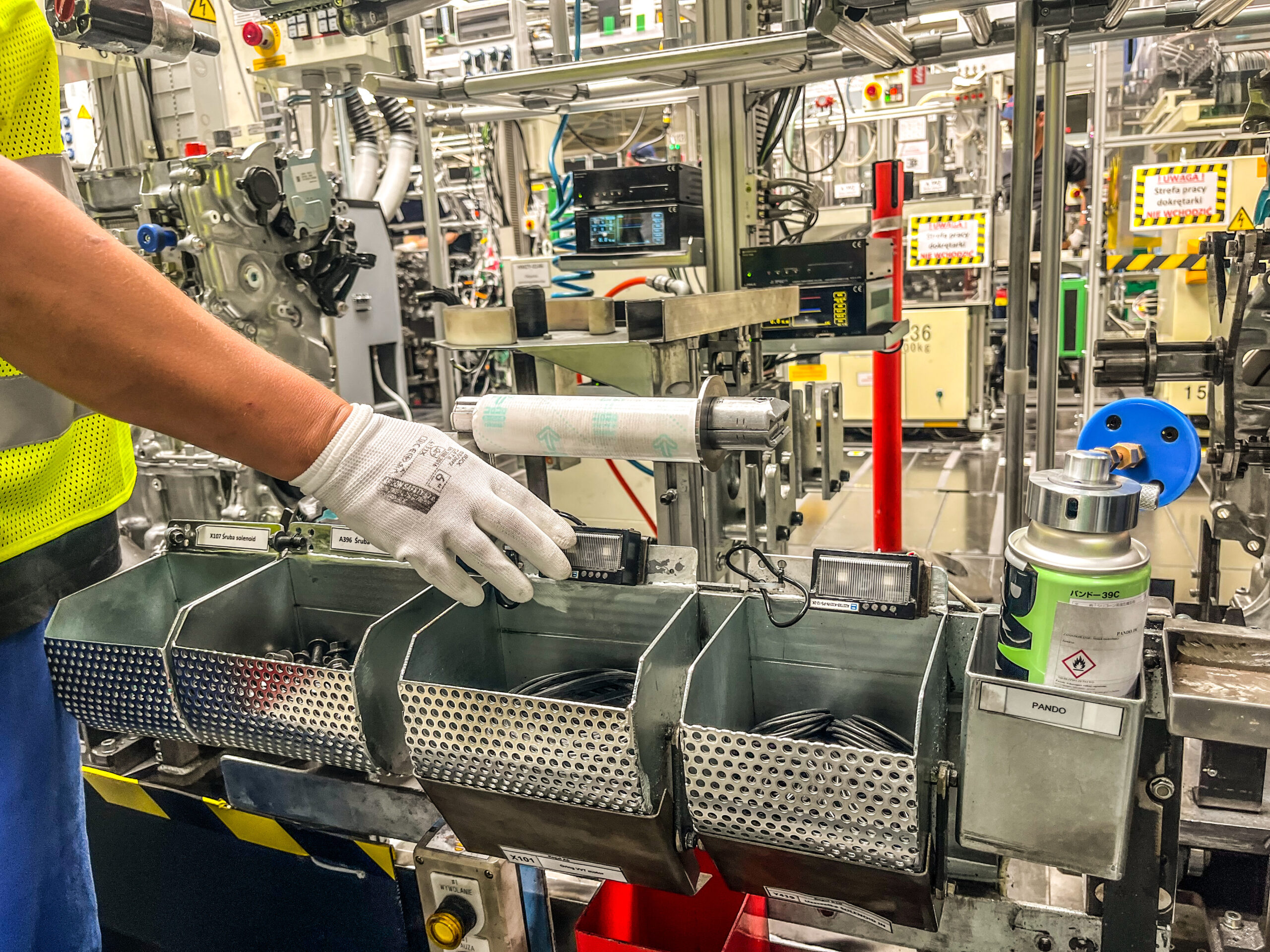
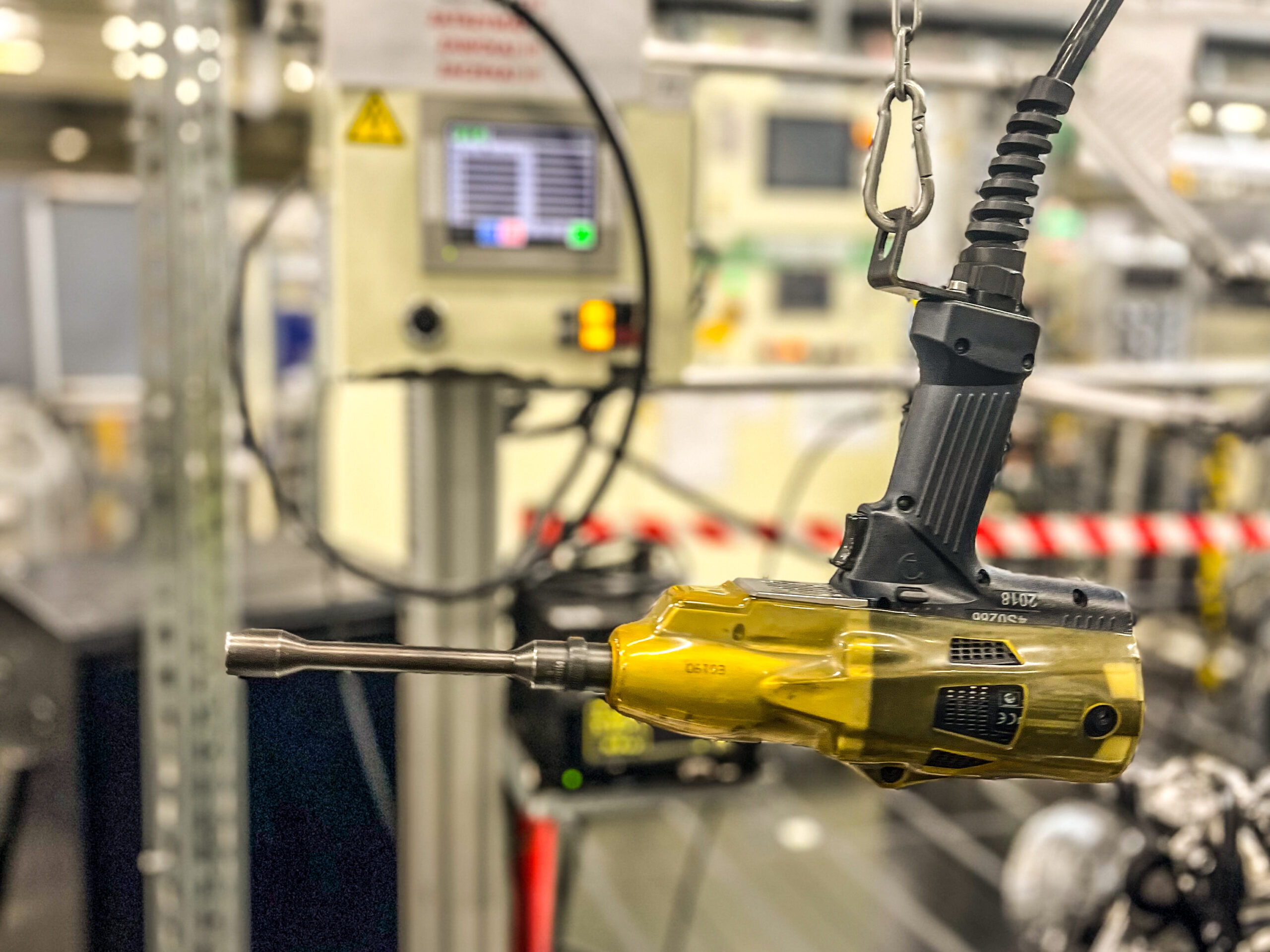
ANDON: SZYBKIE REAKCJE I PREZYCYZJNE ROZWIĄZANIA W TPS
Andon (z j. japońskiego oznacza „lampion”) to w fabrykach Toyoty system zawiadomienia wizualnego, który pracownik linii może aktywować poprzez naciśnięcie przycisku. W rezultacie uruchamiany jest sygnał dźwiękowy i świetlny, który wskazuje miejsce wystąpienia problemu na tablicy informacyjnej. Andon umożliwia szybką reakcję, jest łatwy do dostrzeżenia i minimalizuje ryzyko powstania wadliwego silnika.
Wszystkie stanowiska są wyposażone w dwa przyciski: jeden odpowiedzialny za aktywację wizualnego systemu, a drugi odpowiedzialny za zatrzymanie linii. U nas każdy pracownik może użyć Andonu, gdy:
- odczuwa niepewność;
- zauważa, że jakiś błąd przeszedł na wcześniejszym etapie produkcji;
- popełnił błąd.
Dźwięk oraz symbol na ekranie są gwarancją, że lider obecny na hali nie przeoczy miejsca wykrycia nieprawidłowości oraz że szybko dotrze w odpowiednie miejsce. Pracownik może dalej zajmować się swoją pracą, bo nie ma potrzeby opuszczania stanowiska, żeby porozmawiać z liderem. W momencie, gdy ten pojawi się przy stanowisku, zaczyna rozmawiać z pracownikiem o powodzie użycia Andonu. Analizuje sytuację i jeśli jest w stanie, to rozwiązuje ją od ręki, a jeśli nie, to udaje się z tym do odpowiednich osób na wyższych stanowiskach.
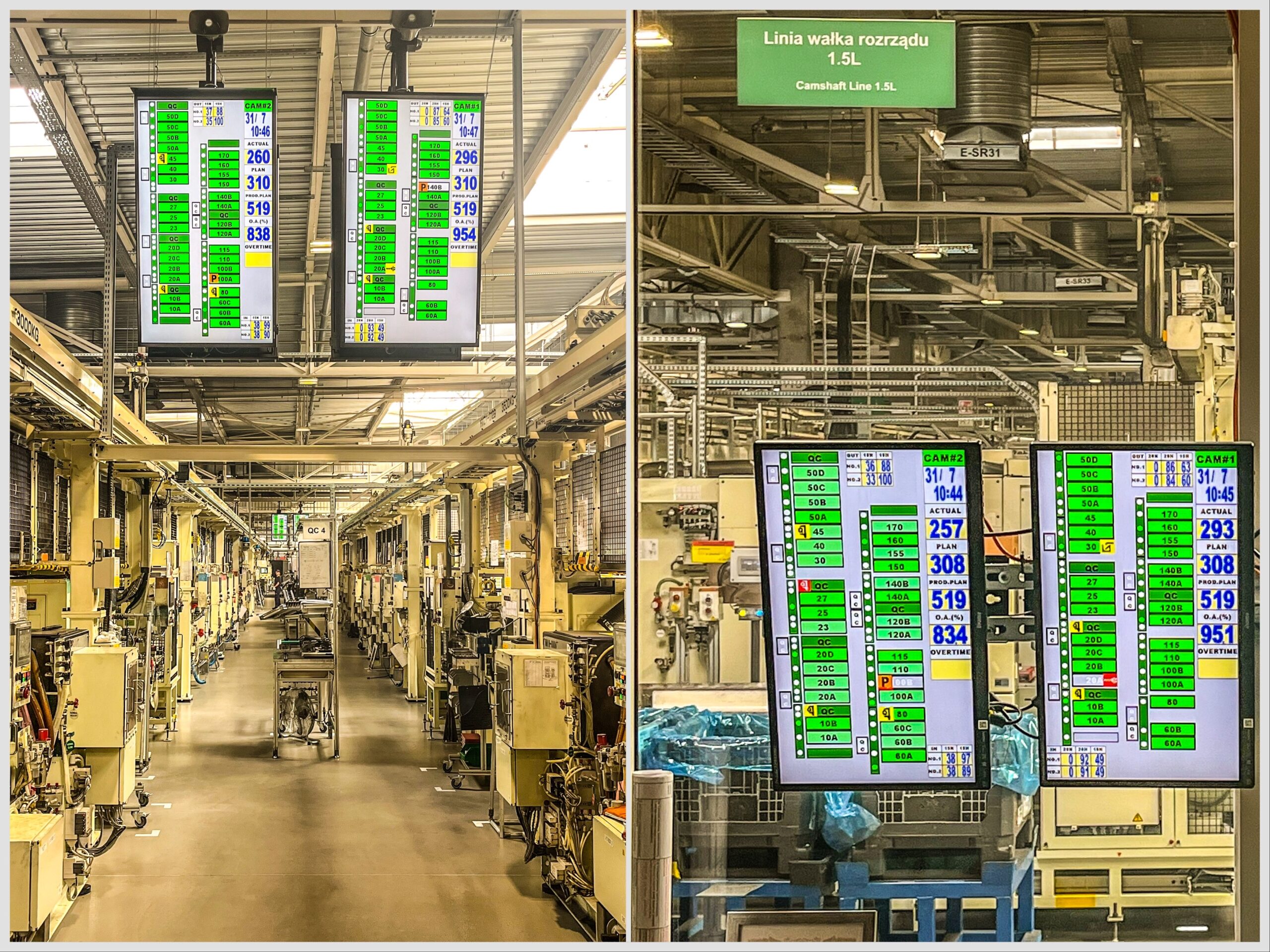
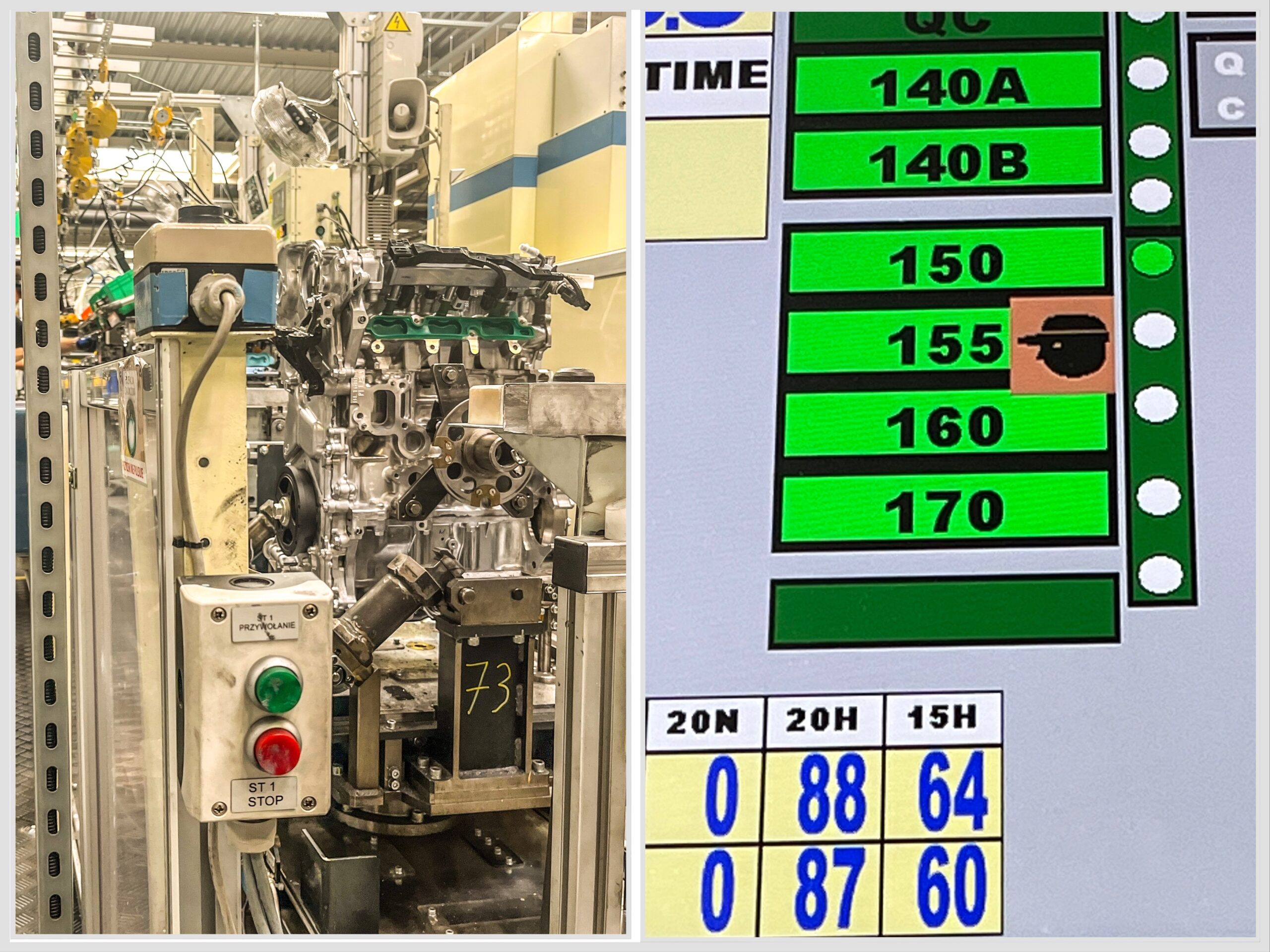
A już wkrótce na naszym blogu pojawi się druga część artykułu poświęconego projektowi LATO i Systemowi Produkcyjnemu Toyoty. 😊