EPKM, czyli jak wdrożyć KAIZEN w praktyce
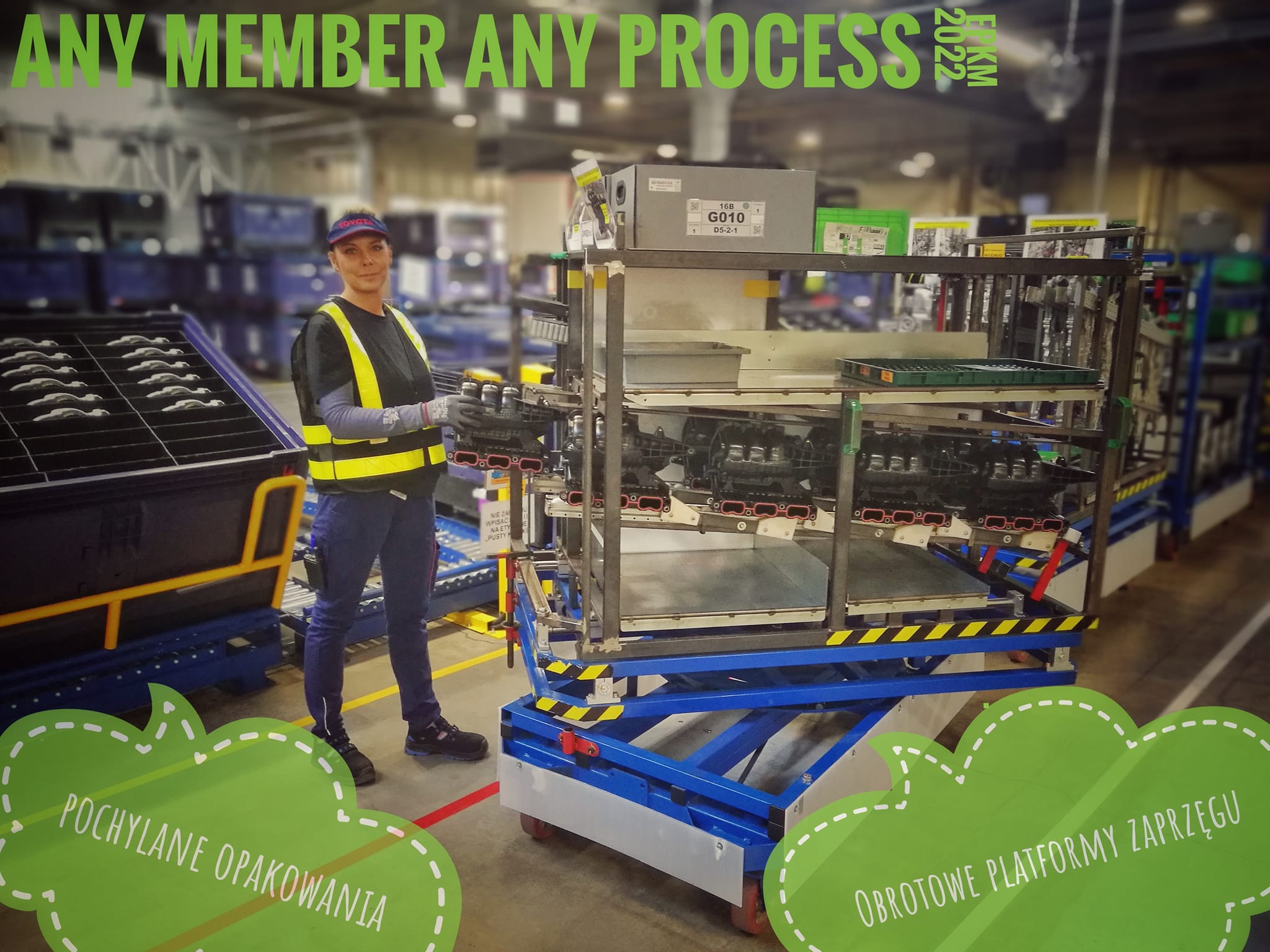
EPKM (European Production Kaizen Meeting) to coroczne spotkanie przedstawicieli wszystkich europejskich fabryk Toyoty. We wrześniu 2022 r. gospodarzem EPKM była nasza fabryka w Wałbrzychu, a dyrektorzy produkcji z całej Europy mogli obejrzeć m.in. usprawnienia, które w swoim dziale wprowadzali Jordan i Ola.
Praca, która nie jest optymalnie rozplanowana, nieraz całkiem dosłownie może stać się ciężka. Dlatego w Toyocie wprowadzamy działania kaizen. Czym są? Najkrócej rzecz ujmując, to rozwiązania mające na celu usprawnienie naszej pracy. I to właśnie o nich mówiliśmy podczas wydarzenia. Jak poduszki powietrzne pomogły nam odciążyć pracowników? Jakie roboty pojawiły się w naszej fabryce i czym się zajmują? Czy kobiety w fabryce Toyoty mogą pracować nad każdym procesem? I w końcu – jak działa kaizen w praktyce? O tym wszystkim opowiadają członkowie naszej załogi, Jordan i Ola.
Jordan: Wszystkie procesy powinny być przyjazne dla każdego pracownika
Czas ostatniego EPKM-u i przygotowania do niego był szczególnym okresem dla całej hali TNGA#3 (produkcja silnika TNGA). Dlaczego? Ponieważ z jednej strony było to pierwsze tak ważne wydarzenie w historii produkcji, z drugiej zaś – dużą część zespołów stanowią osoby z małym doświadczeniem w TMMP.
Nie inaczej było w przypadku logistyki wewnętrznej. Dodatkowo w naszym, dotąd męskim zespole, zaczęły pracować panie. To dla nas niezwykle ważna zmiana, którą dobrze opisuje hasło: „Any Member, Any Process” („Dowolny proces dla dowolnego pracownika”). W praktyce oznacza to, że wszystkie procesy powinny być przyjazne dla każdego pracownika. Niezależnie od jego wzrostu, wieku, wagi czy innych indywidualnych uwarunkowań. Wdrożyliśmy szereg usprawnień, które poza ergonomiczną unifikacją stanowisk przyniosły realne obniżenie kosztów. To wyjątkowo istotne szczególnie na dzisiejszym rynku automotive.
Poduszki idealne do… pracy
Dostarczanie części na obrotowych platformach pozwoliło zastosować rozwiązania „Touchless”, które obniżyły przenoszoną wagę, oraz „Touch&Go”, co skróciło czas operacji. Poduszki powietrzne, pochylające skrzyniopalety z dużymi częściami, wyeliminowały konieczność schylania się. Taką technologię wprowadziliśmy dla wszystkich dużych części, które stanowią blisko 35% transportowanego ciężaru wśród wszystkich części montażowych. Najcięższa z nich – koło zamachowe – waży ponad 9 kg i trzeba było je wyciągać z boxa aż 250 razy na zmianę!
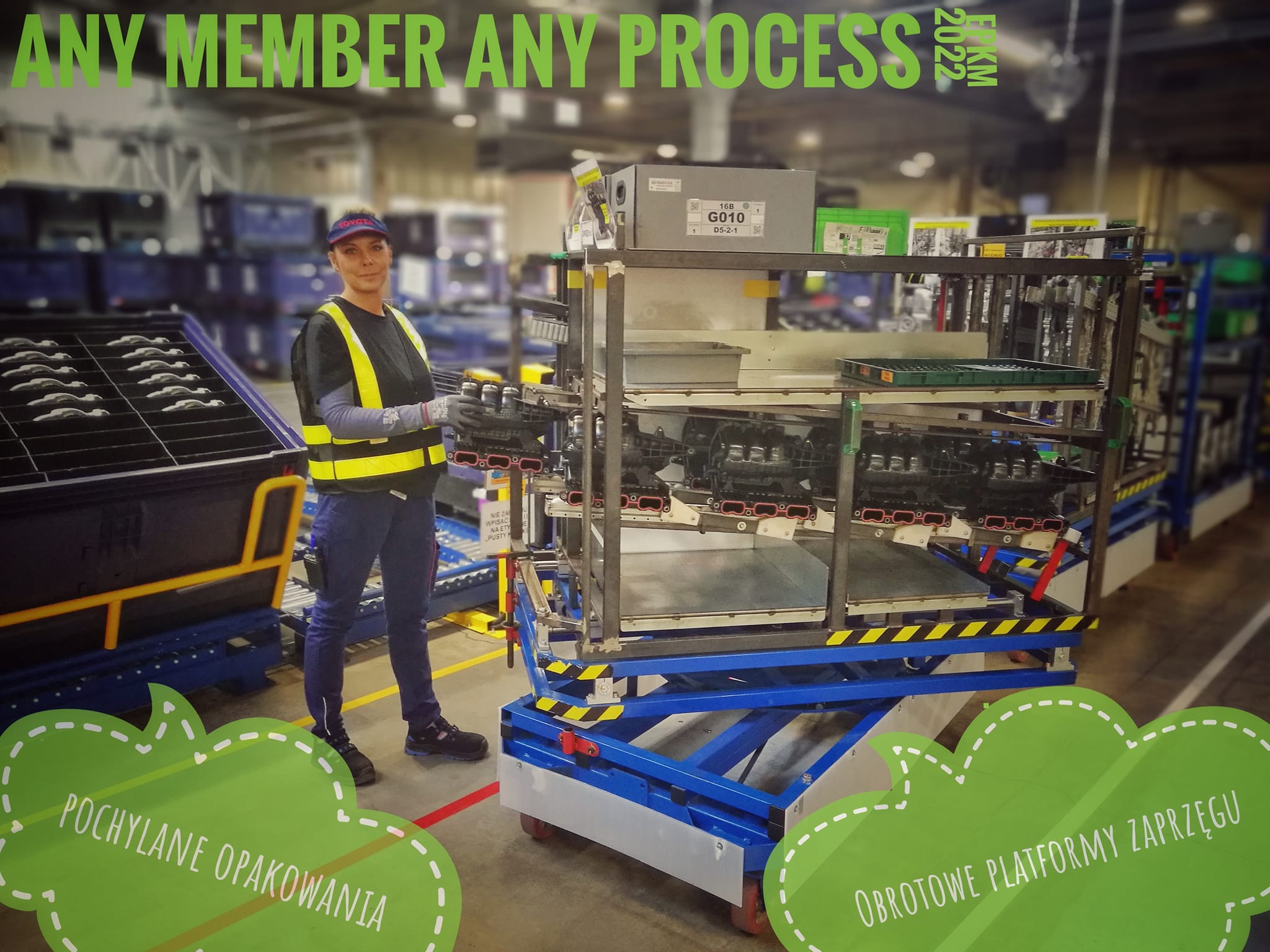
Wraz z EPKM-em zawitała do nas digitalizacja. Do procesu załadunku na zaprzęg części na montaż wprowadziliśmy skanowanie jako poka-yoke. To rozwiązanie eliminuje możliwość dostarczenia niewłaściwej części. To bardzo istotne przy częściach podobnych. Już dzisiaj myślimy o produkcji kolejnego typu silnika TNGA. W ramach cyfryzacji procesów postawiliśmy dwa roboty. Jeden z nich ładuje surowe bloki i głowice na wózki AGV, drugi odbiera wyroby gotowe z linii. To pierwsze na świecie takie rozwiązanie w przypadku silników Toyoty.
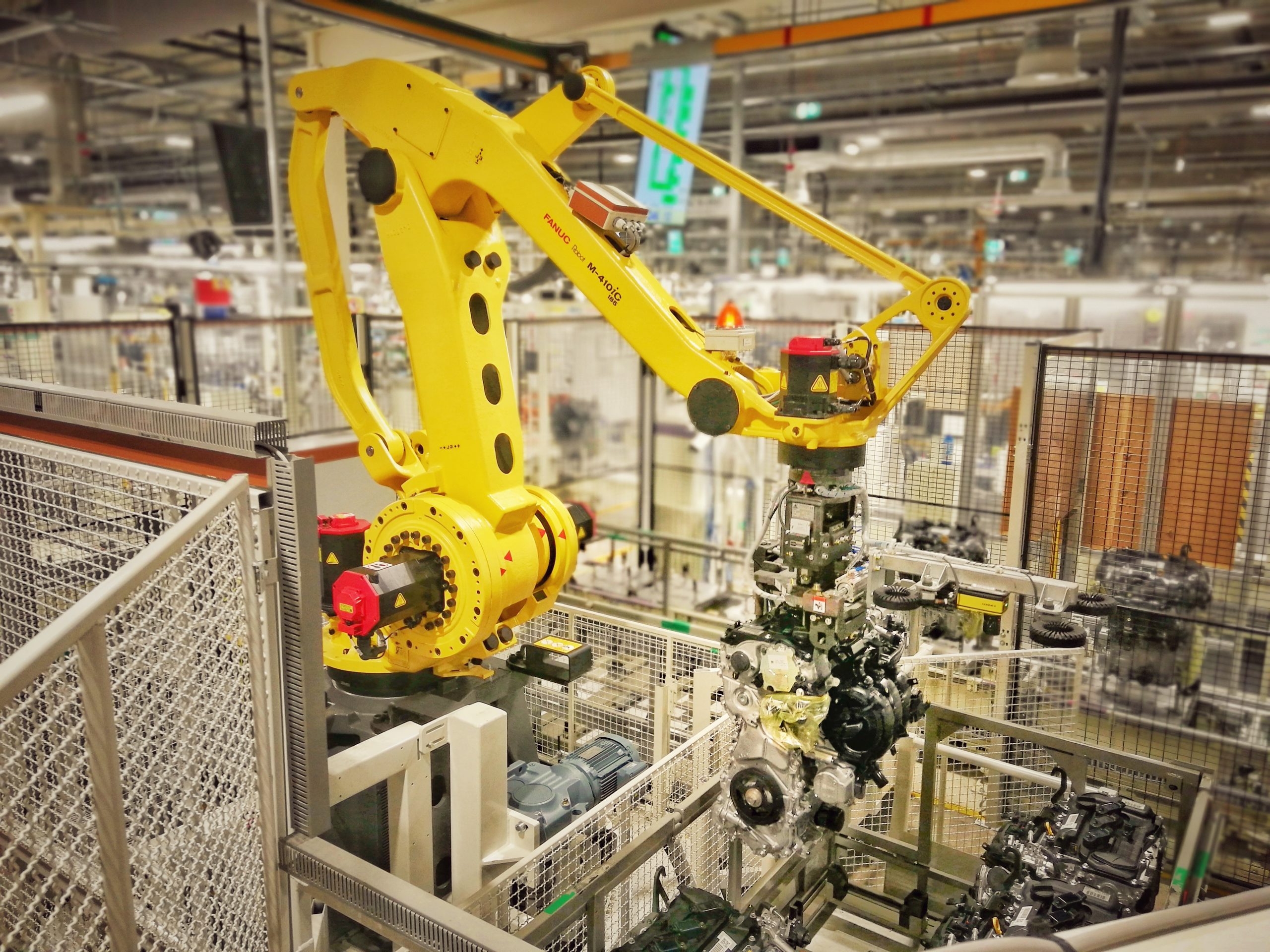
W ramach działalności „Shop by Shop” („Hala po hali”) przejęliśmy od montażu transport międzyprocesowy wałków rozrządu. Z uwagi na to, że jako logistyka dostarczamy części w to samo miejsce, do którego pracownik montażu woził wałki wózeczkiem produkcyjnym, mogło tu dochodzić do kontaktu człowiek-maszyna. Tutaj także zastosowaliśmy rozwiązania „Touchless” oraz „Touch&Go”.
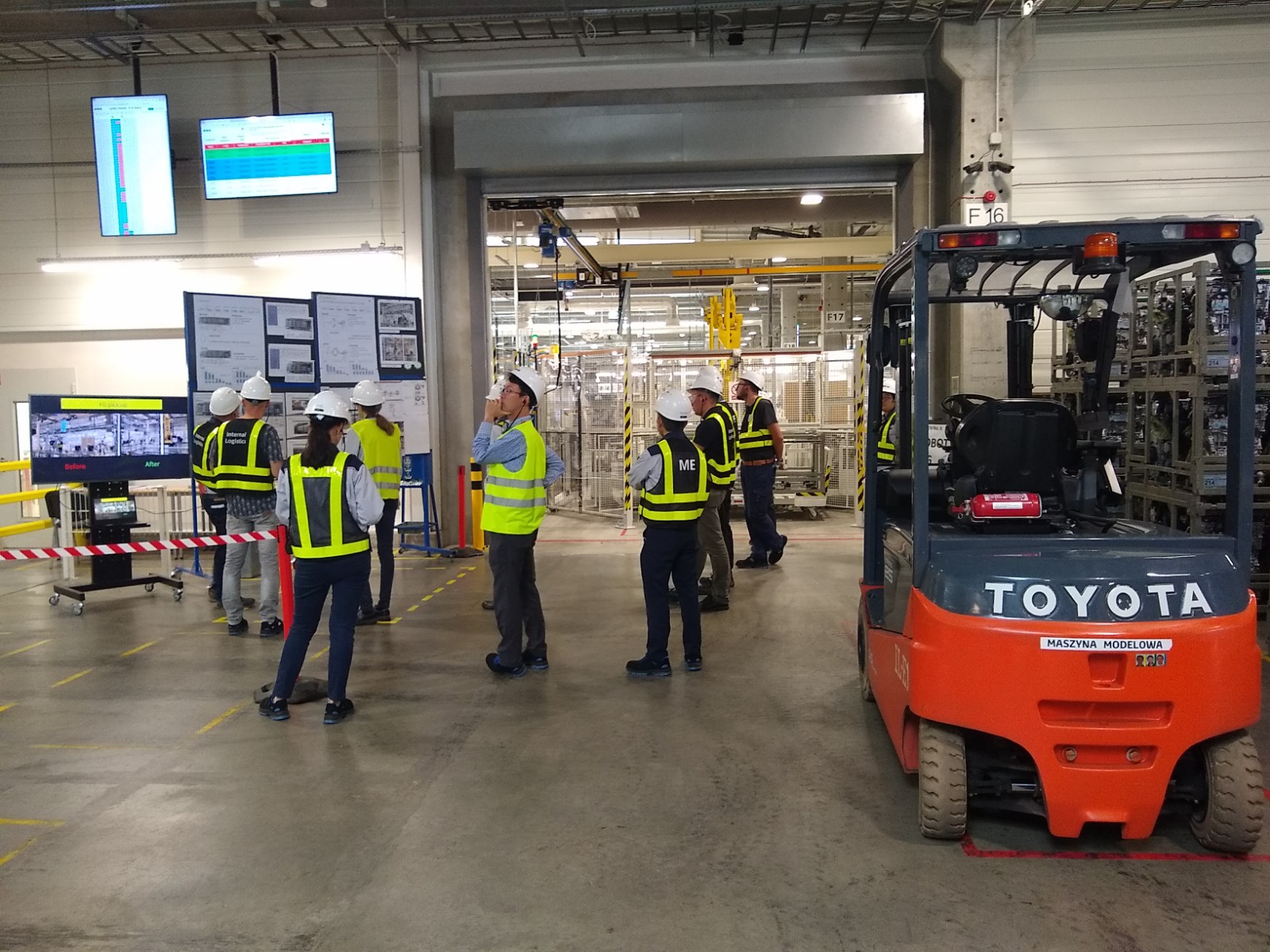
Kaizen działa!
Takie przykłady przedstawione podczas EPKM uświadomiły młodym pracownikom, jak ważne są działania kaizen w praktyce, jaką wagę do tego przykłada Toyota jako całość. Nie jest to cięcie kosztów, a przede wszystkim ułatwienie naszej wspólnej pracy. Dla mnie było to duże wyróżnienie, bo mogłem zaprezentować jedno z rozwiązań. Dziękuję wszystkim, którzy przyczynili się do naszego wspólnego sukcesu. I nie zapominamy, by działać dalej – we can do it!
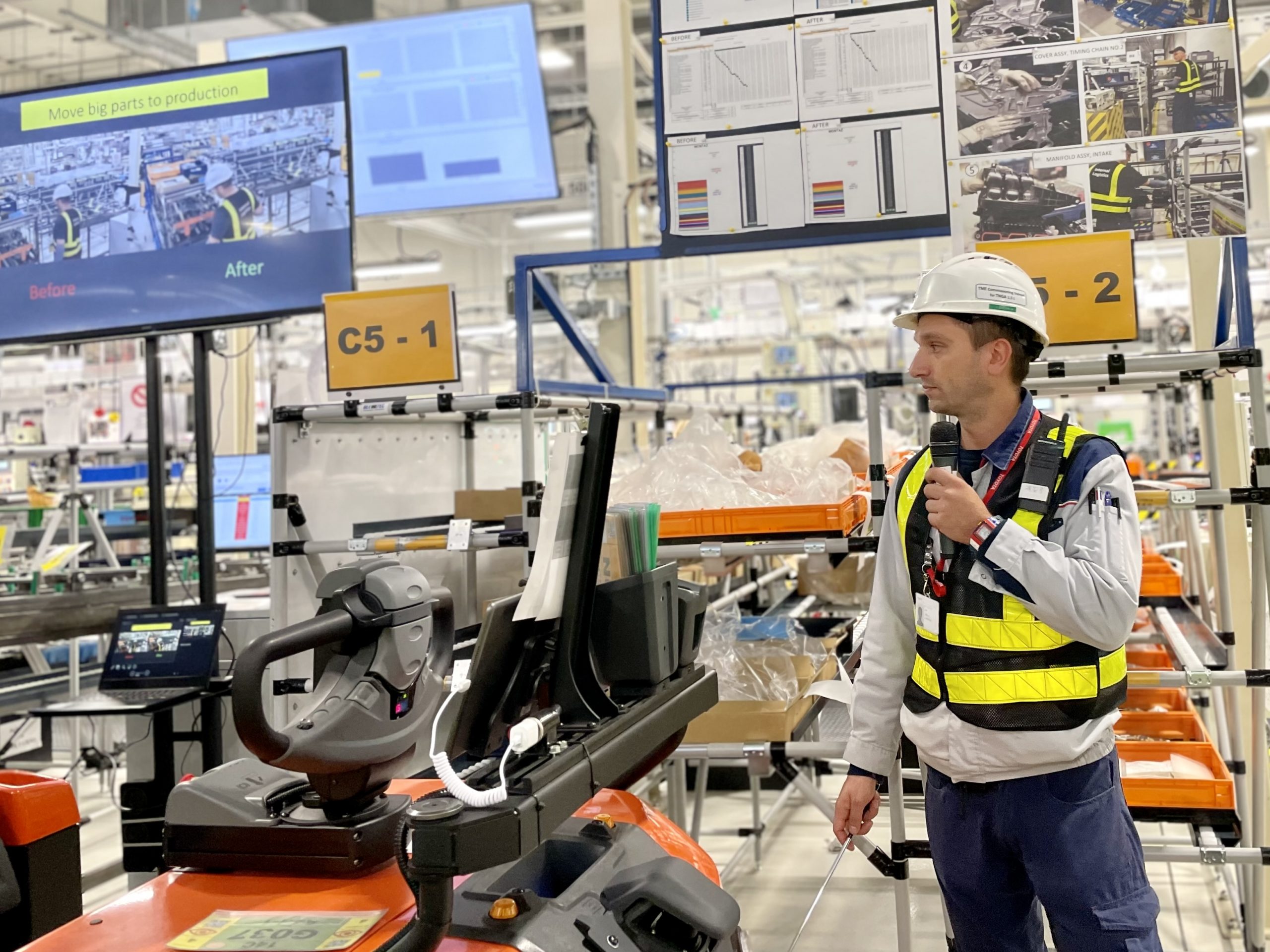
Ola: W przeszłości kobiety nie mogły pracować w logistyce
Do logistyki trafiłam w marcu 2022 r., jako jedna z pierwszych kobiet w tym obszarze. Jeżdżę tzw. zaprzęgami, którymi dostarcza się części na linie, a także wózkiem widłowym na dostawach i wysyłkach. Odpowiednie uprawnienia już miałam, ale w przeszłości kobiety nie mogły pracować w logistyce ze względu na normy BHP i na przykład zbyt duże ciężary, które tu trzeba było przenosić.
Dlatego wprowadzono tu różne usprawnienia, które pokazywaliśmy na ostatnim EPKM. Na przykład na moim stanowisku mogłam zaprezentować obrotowe zaprzęgi, dzięki którym zredukowano potrzebę prac ręcznych i zmniejszono potrzebę przenoszenia ciężarów. Na moim stanowisku wyeliminowaliśmy też potrzebę ręcznego przekładania pustych i pełnych pudełek z częściami – wałkami, które ważą 12-13 kg. Teraz jedną dźwignią przenoszę je z miejsca na miejsce.