Co się dzieje w fabrykach Toyoty, gdy mamy „shutdown”?
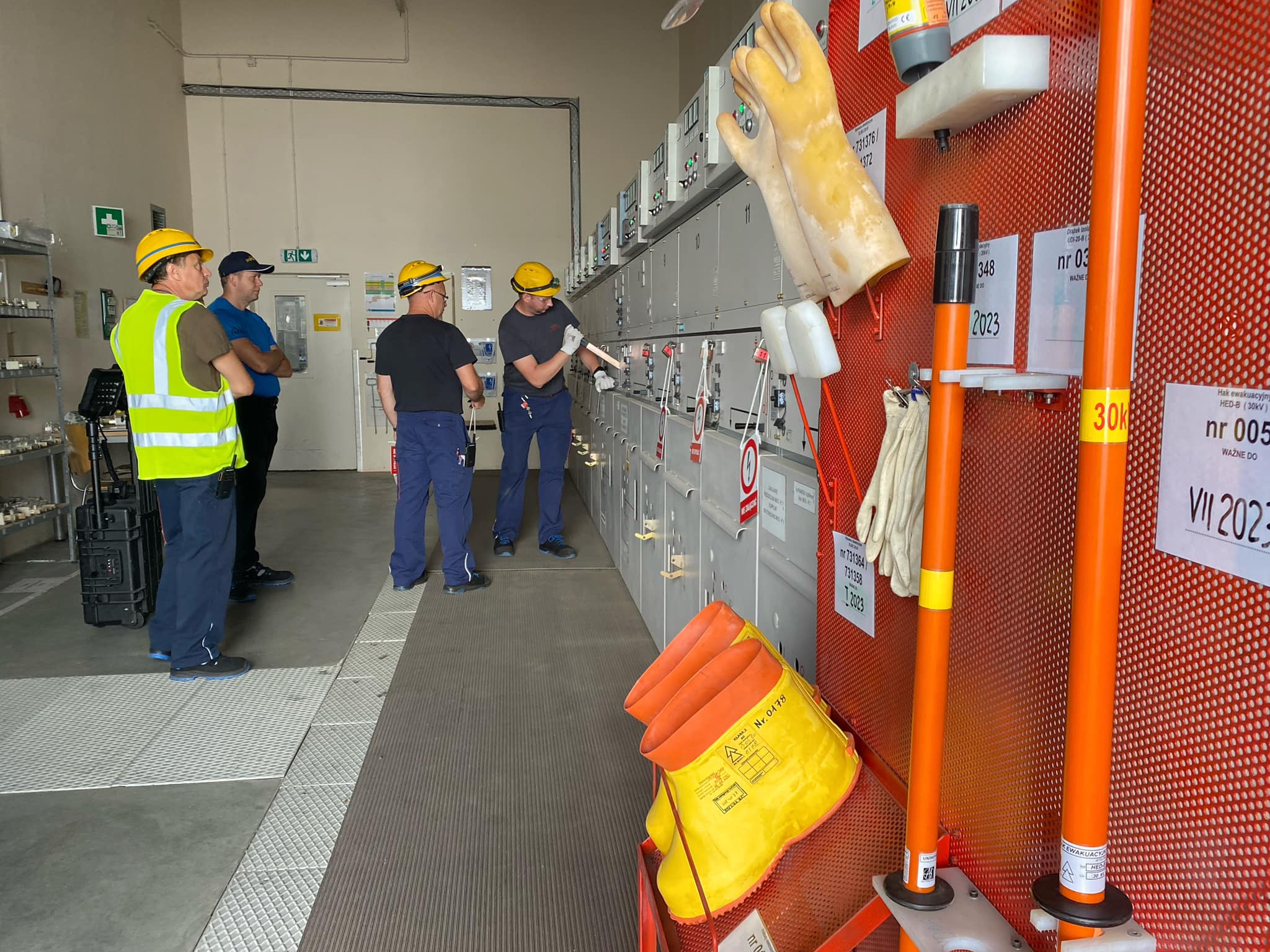
Dlaczego nasi pracownicy mają „grupowy” urlop w sierpniu? Z czym wiąże się ta przerwa produkcyjna i dlaczego się na nią decydujemy? Na te i inne pytania odpowiadają Michał (z Wałbrzycha) i Marcin (z Jelcza-Laskowic).
Zacznijmy od początku – co roku, w sierpniu, fabryki Toyoty w Polsce (w Jelczu-Laskowicach i Wałbrzychu) mają przerwę produkcyjną, znaną wewnętrznie jako „shutdown”. Większość pracowników podczas niej jest nieobecna, lecz zdarzają się wyjątki. Wyjątki, które koordynują niezbędne usprawnienia i modyfikacje procesów produkcji. Jesteście ciekawi, jak to wygląda? Przenieśmy się więc do Wałbrzycha, a dokładniej do wałbrzyskiej fabryki Toyoty.
Michał, manager działu Karakuri i ME (Manufacturing Engineering – Inżynieria produkcji) w obszarze manualnych skrzyń biegów oraz silników benzynowych opowiedział o zmianach, które miały miejsce podczas tego czasu.
PRZENOSZENIE PALETKI
Michał: Jako pierwszy, usprawniony proces, weźmy na tapet proces polegający na ręcznym przenoszeniu paletki na linii podmontażu bloku. Dokładnie – ręcznym przenoszeniu paletki. A teraz? Robot wykonuje cięższą pracę samodzielnie, dzięki czemu to stanowisko stało się mniej obciążające pracownika. Ergonomicznie niewygodna praca została wyeliminowana.
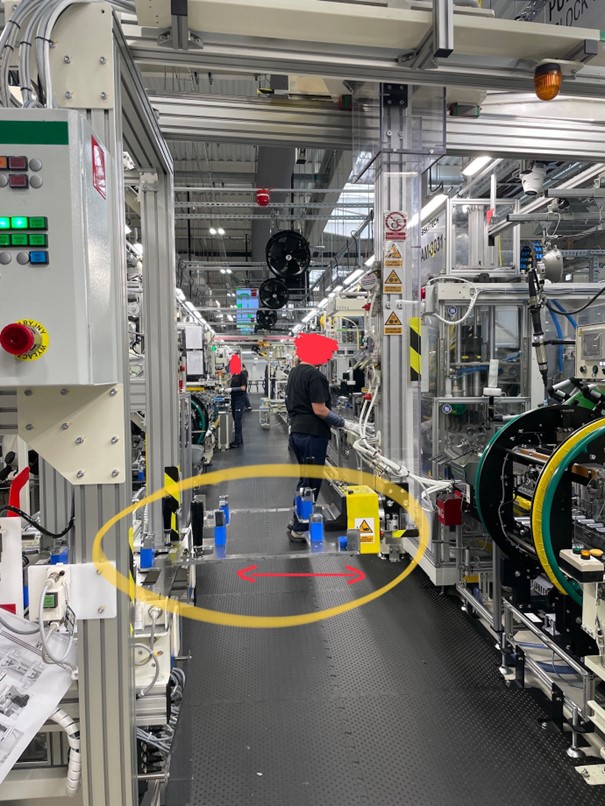
OBROTNICA BLOKU
Kolejnym procesem, który został usprawniony, to obrotnica bloku. Do tej pory obrót bloku w celu zeskanowania numeru części, wykonywany był przez pracownika. Obrotnica przez swój rozmiar i ciężar sprawiała problemy naszym pracownikom. Po jej zautomatyzowaniu, obrót silnika wykonuje się samodzielnie. Operator nie musi się już siłować z obrotem detalu.
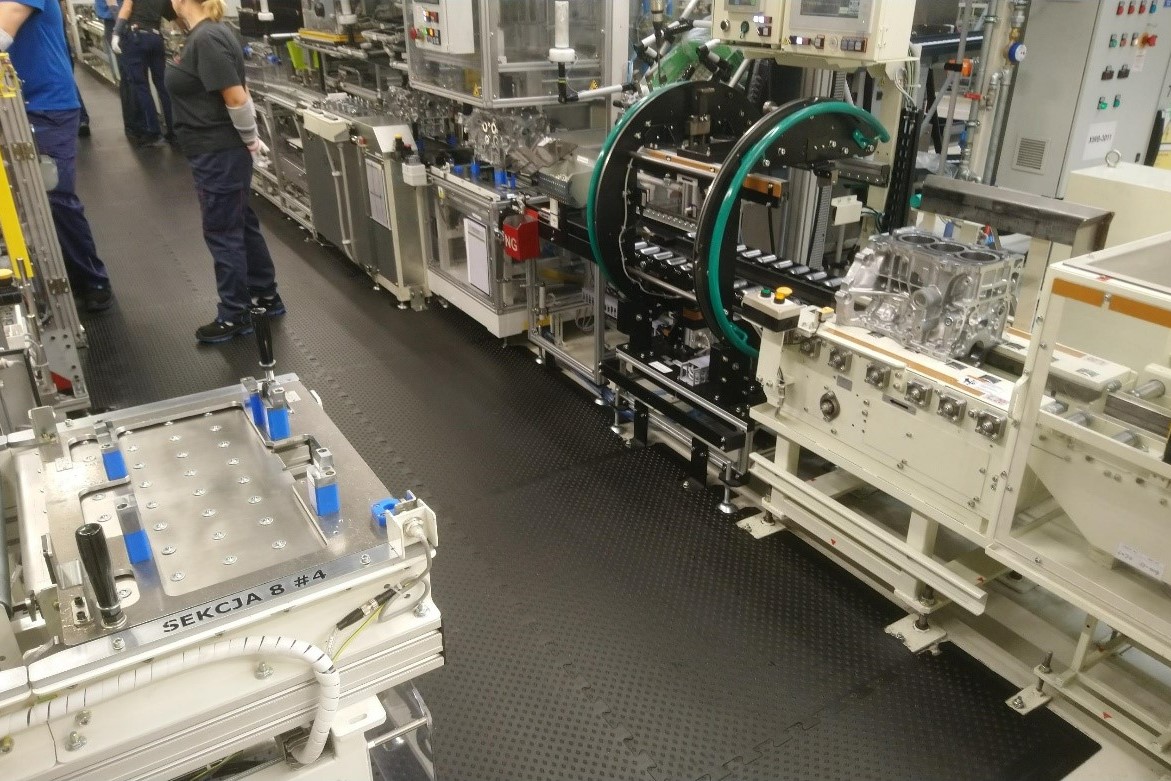
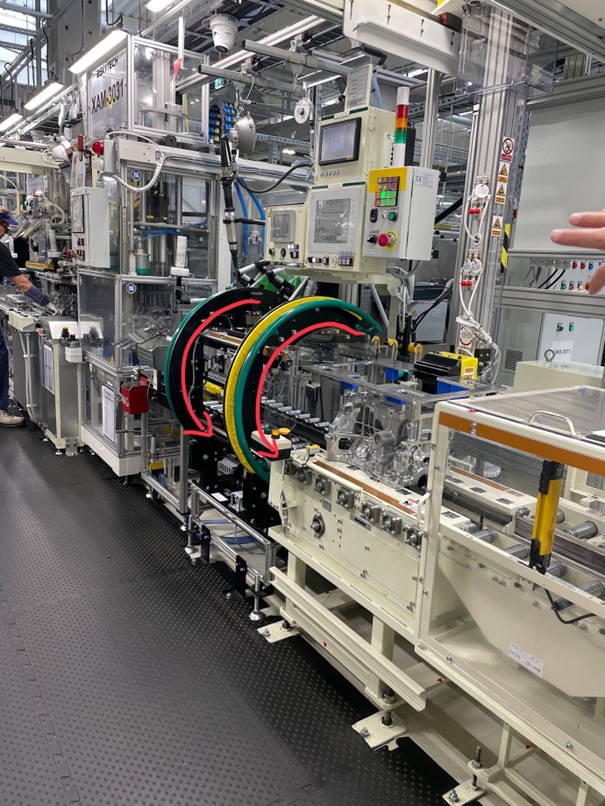
POBIERANIE STÓP WAŁU KORBOWEGO
Trzecim usprawnieniem jest automatyzacja procesu pobierania stóp wału korbowego manualnym manipulatorem. Bazując na rozwiązaniu z Jelcza, proces został całkowicie zautomatyzowany. Ruchy manipulatora, które do tej pory wykonywał pracownik, zastąpione zostały siłownikami pneumatycznymi. Operator nie musi już trzymać dłoni na rączkach maszyny, sterując nią, w niewygodnej wysokiej pozycji. Dzięki temu wyeliminowano konieczność ręcznego obniżania maszyny, co skutkuje eliminacją obciążenia operatora.
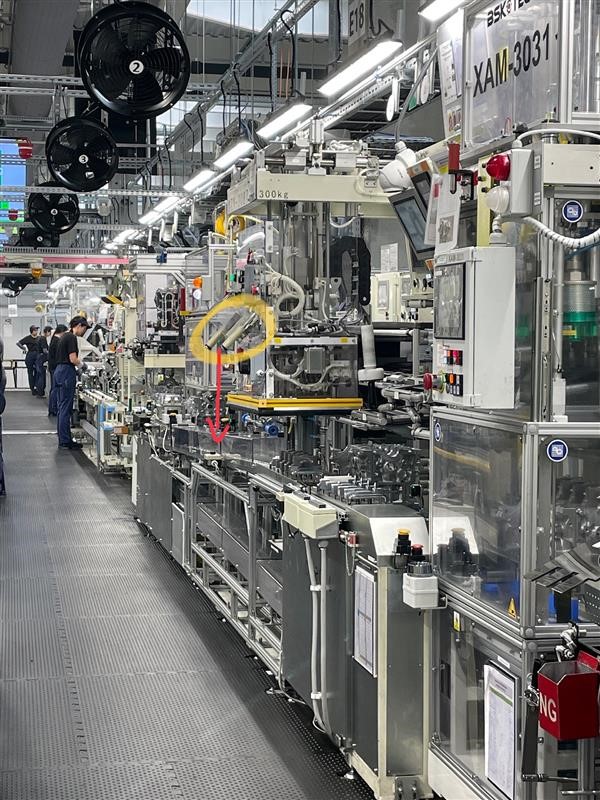
PROCES DOKRĘCANIA DYSZEK OLEJOWYCH
Kolejnym usprawnionym procesem jest proces dokręcania dyszek olejowych. Trzy dyszki olejowe dokręcane były do tej pory manualnie. Operator musiał wcelować kluczem w śruby mocujące dyszki w bloku silnika. Zastosowaliśmy rozwiązanie z projektu KR (silników benzynowych) i zautomatyzowaliśmy proces tworząc prostą i energooszczędną maszynę, która zautomatyzowała proces dokręcania.
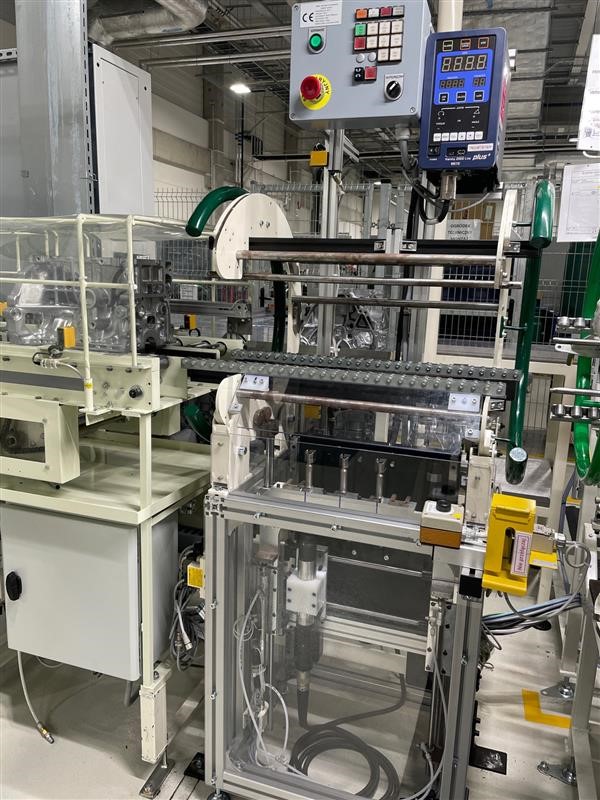
ZAŁADUNEK SILNIKÓW
Największą zmianą na hali TNGA (silników nowej generacji) jest proces załadunku silników na paletę, który teraz zamiast człowieka wykonuje duży robot, czyniąc ten proces w pełni zautomatyzowanym. Następnie silniki są odbierane przez logistykę. Robot przygotowany został przez dział TME UPE (Dział inżynieryjny Toyota Motor Europe).
Jesteście ciekawi jak działa? 😊 Zapraszam do obejrzenia filmiku.
WSPÓŁPRACA Z ROBOTEM
Wiedzieliście, że jest możliwość interakcji człowieka z robotem? Podczas procesu dokręcania śrub stopek wałków rozrządu zainstalowano cobot, czyli robot, który współpracuje z ludźmi – operator podaje detal cobotowi, on dokręca śruby i oddaje detal z powrotem pracownikowi do wykonania kolejnych operacji montażu.
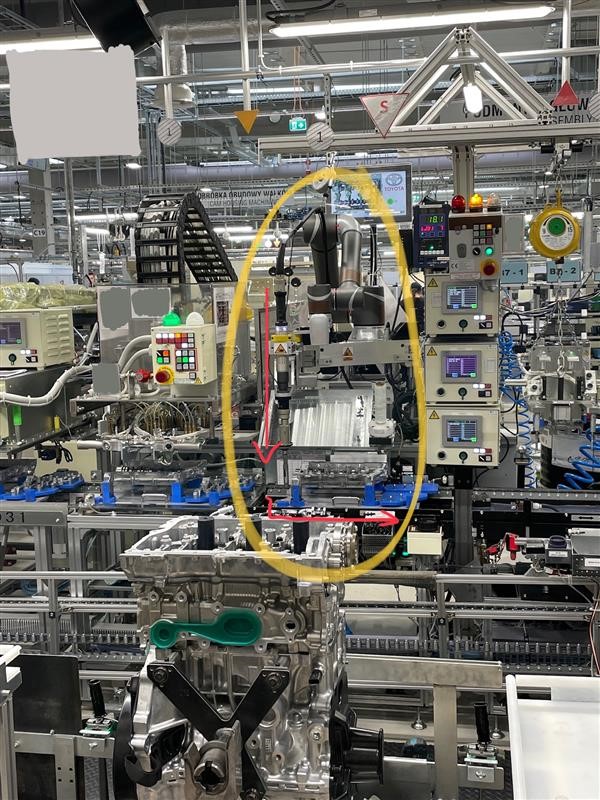
SHUTDOWN W JELCZU-LASKOWICACH
Marcin: Dla Jelcza to był dość „spokojny” shutdown. Pierwszy raz od wielu lat bez większych prac budowlanych, bez demontażu dużych maszyn czy całych linii produkcyjnych. Nie oznacza to jednak, że niewiele się działo. Zaszło kilka istotnych zmian, których nie widać na pierwszy rzut oka.
MODYFIKACJE NA LINIACH
Największym projektem jest modyfikacja sposobu dostarczania silników z linii montażu na linię testów. Celem projektu była poprawa efektywności transportu. Dzięki modyfikacji podajników skrócono drogę przejazdu AGV (pojazdu autonomicznego). To pozwoliło na redukcję ilości AGV oraz zmniejszenie ryzyka kolizji z transportem części na linię.
Zmiany wprowadzono również na linii obróbki. Na linii Camhousingu (pokrywie wałków rozrządu) zainstalowano nowego robota współpracującego, który podaje i wkłada śruby do camshousingu.
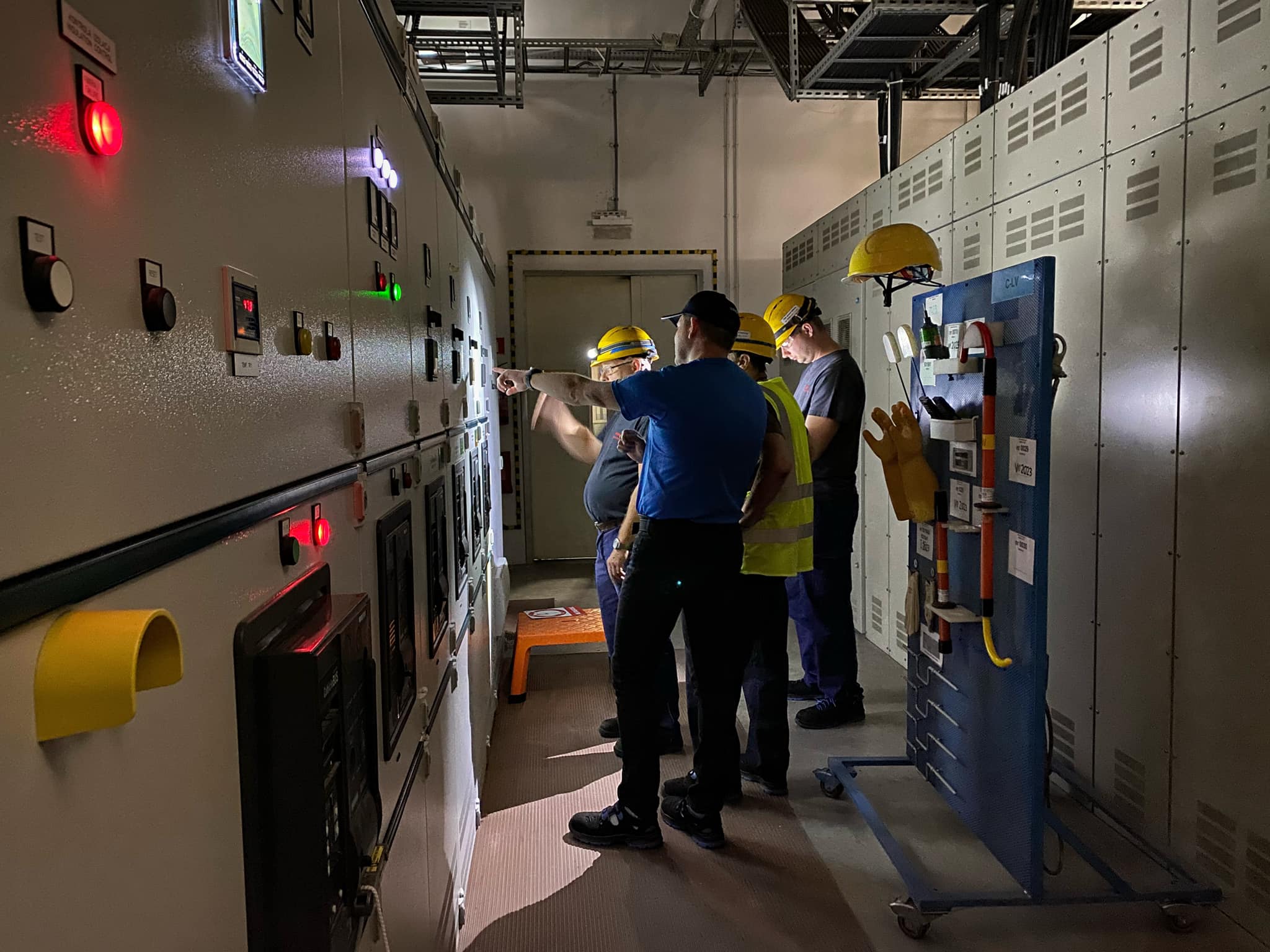
AUTOMATYZACJA NA WYŻSZYM POZIOMIE
Prace nad automatyzacją procesu prowadzone też były na odlewni. Teraz drzwi maszyn linii Finishingu zamykają się automatycznie. Pozwoliło to poprawić ergonomię na stanowiskach pracy oraz wpłynęło na poprawę czasu cyklu pracy. Były też prowadzone intensywne próby i testy pracy nowych robotów odbierających rdzenie. Inżynierowie mają teraz wiele cennych danych do dalszej pracy.
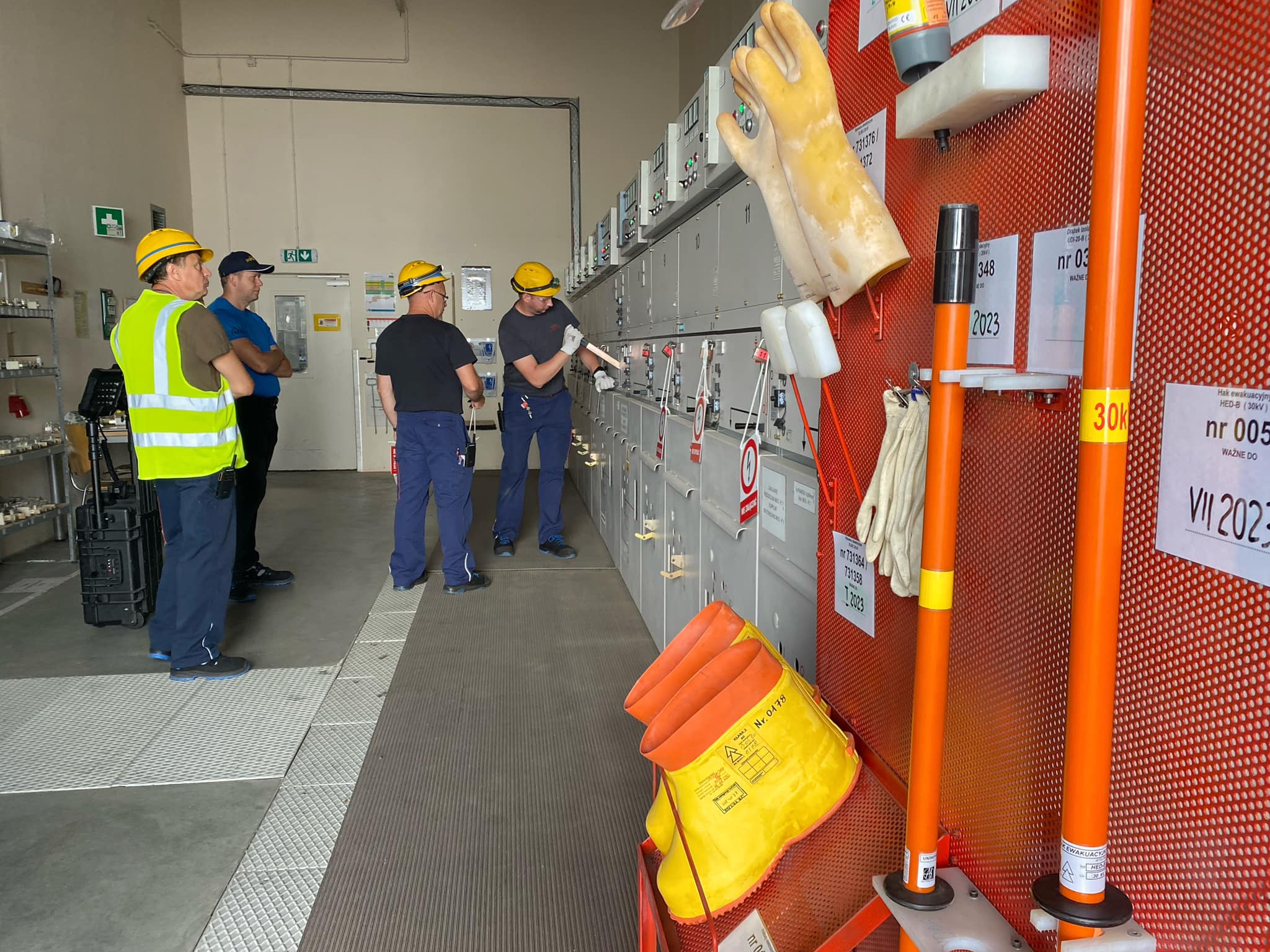
Jeśli chodzi o prace budowlane to kontynuowaliśmy remont toalety przy obszarze logistyki, trwała też modyfikacja pomieszczenia pod dodatkową serwerownię i prace wykończeniowe przy pomieszczeniu treningowym przy odlewni dla działu SUR.
Jak widzicie, mimo wakacyjnej przerwy, w naszych fabrykach działo się bardzo dużo, ale dzięki temu teraz wszystkim pracuje się jeszcze lepiej. 😉